Panasonic, one of the pioneers of automotive lithium-ion batteries and currently one of the top three EV battery manufacturers (see report for January-July 2021 here), says that its automotive battery business is entering a new phase.
The Japanese company has been engaged in batteries since 1931 and its first lithium-ion cells for automotive (1865-type cylindrical cells) use were introduced in 2006 (mainly for use by Tesla).
“Panasonic’s cylindrical lithium-ion batteries were originally designed to deliver outstanding longevity and light weight to notebook PCs, but the emergence of demand for automotive use batteries in the late 2000s led to the development of Panasonic’s automotive battery business”
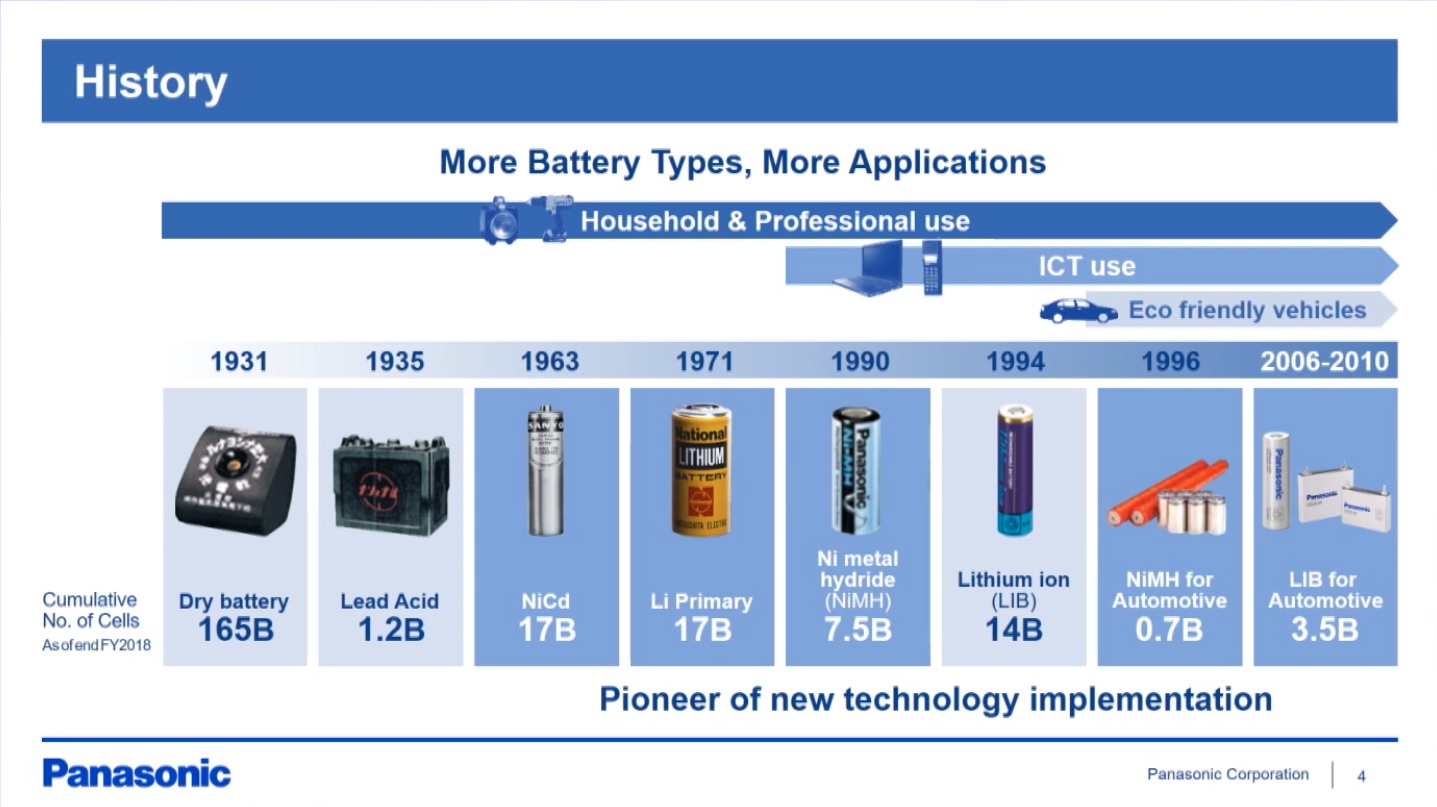
The prismatic cells were offered a little bit later, in 2010.
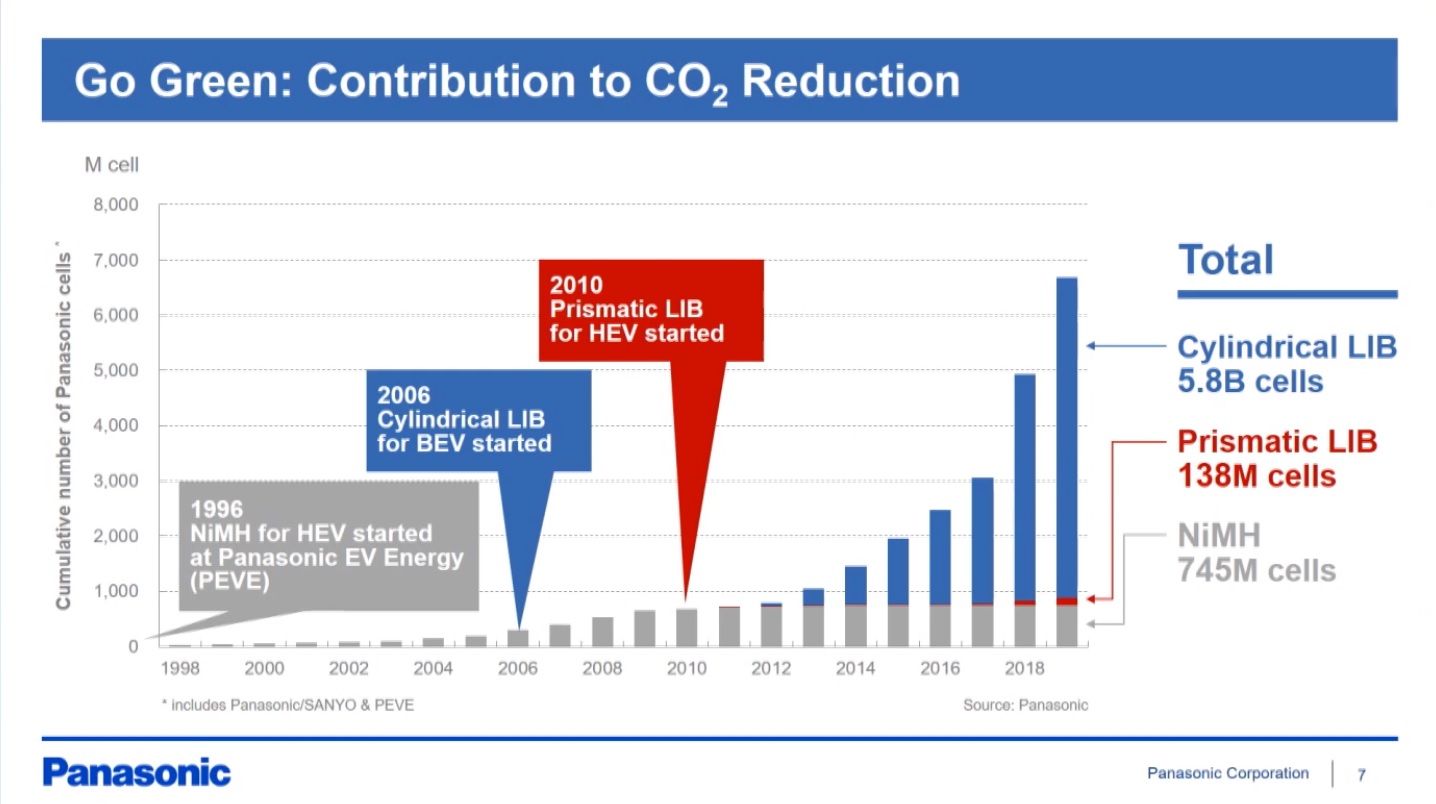
The 1865-type cylindrical cells have a diameter of 18 mm and a height of 65 mm. Panasonic produces this type of cell in Japan and they are still in use in the Tesla Model S/Model X cars (including the latest versions).
In 2017, Panasonic commissioned a manufacturing plant for a new 2170-type of cylindrical automotive batteries at the Tesla Gigafactory in Nevada for use in Tesla Model 3/Model Y and other energy storage products.
The 2170-type have a diameter of 21 mm and a height of 70 mm, which means a noticeably higher capacity per cell.
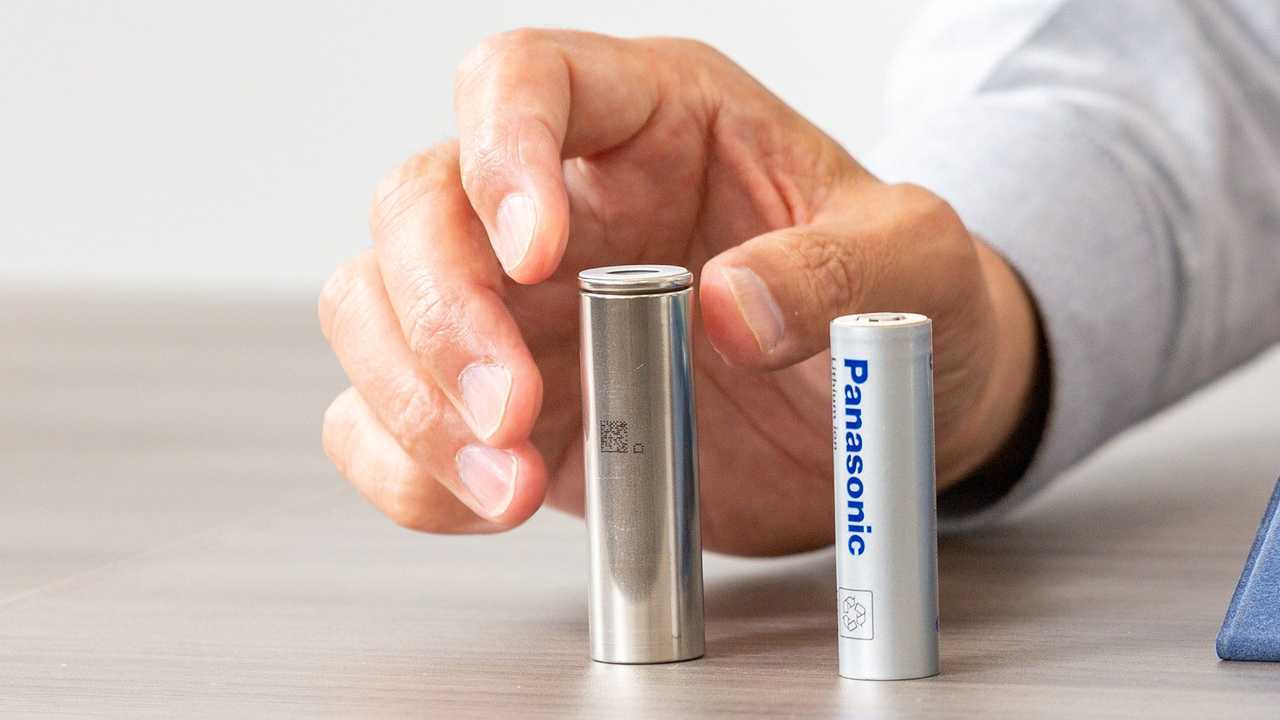
Panasonic Batteries: On the left is the latest 2170, and on the right is the 1865, which is also used in notebook PCs.
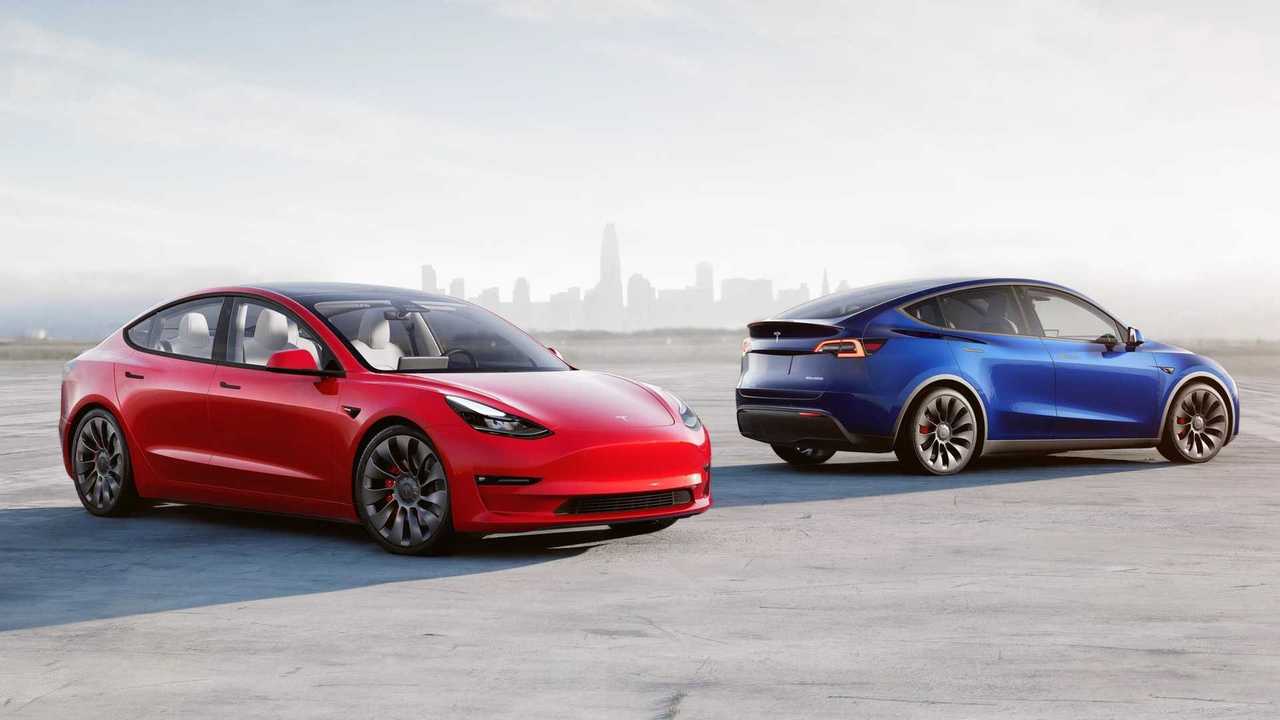
Tesla Model 3 and Tesla Model Y
Shawn Watanabe, Head of Energy Technology and Manufacturing said:
“We set up the North America operation by drawing on the know-how we’ve gained from lithium-ion battery production in Japan–know-how that has allowed us to build a plant that is five times the size and three times the speed of conventional facilities. Due to the nature of the product, we had to meet extremely high standards for safety and quality, and with a new workforce in a location with a different culture and language while also being agile and precise. We couldn’t compromise on any of these points if our goal was uninterrupted production of high-precision batteries.”
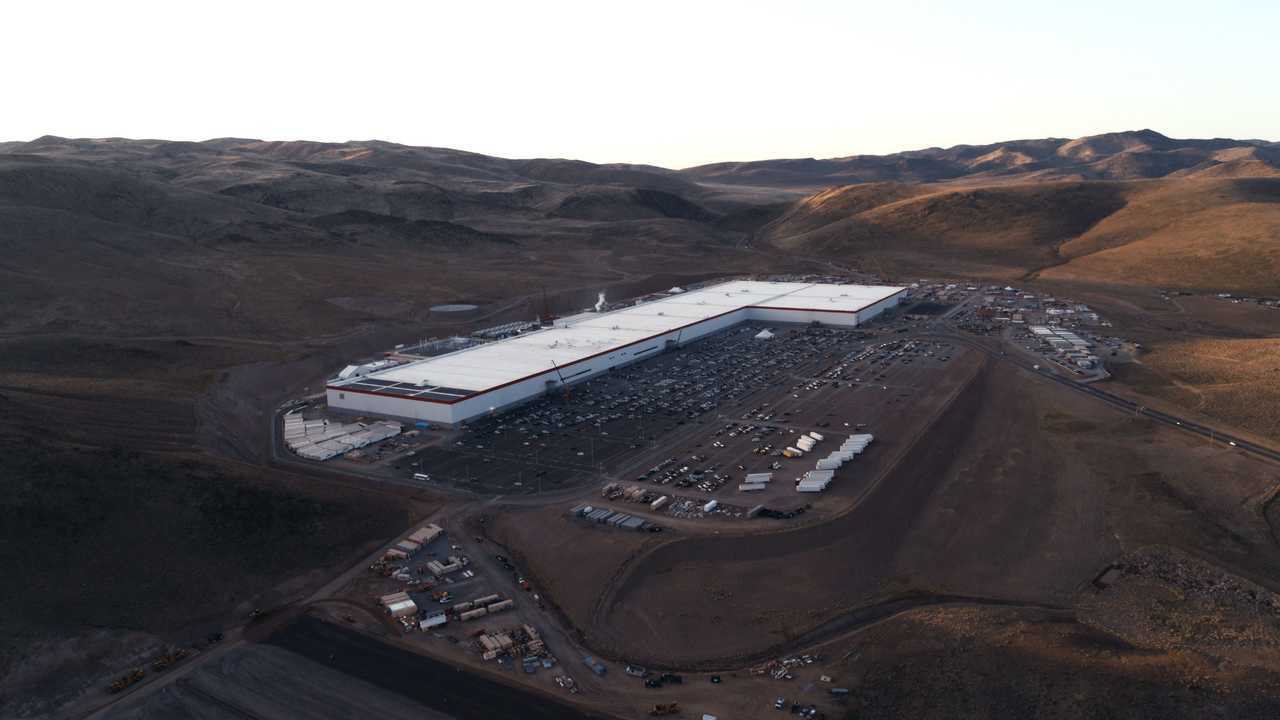
Tesla Giga Nevada (Tesla Gigafactory 1)
So far, Panasonic has produced billions of cylindrical cells and its manufacturing output is still expanding.

According to Shawn Watanabe’s presentation (see video at the bottom), the company has already increased the energy density of its lithium-ion batteries more than three times compared to the original design in 1994.
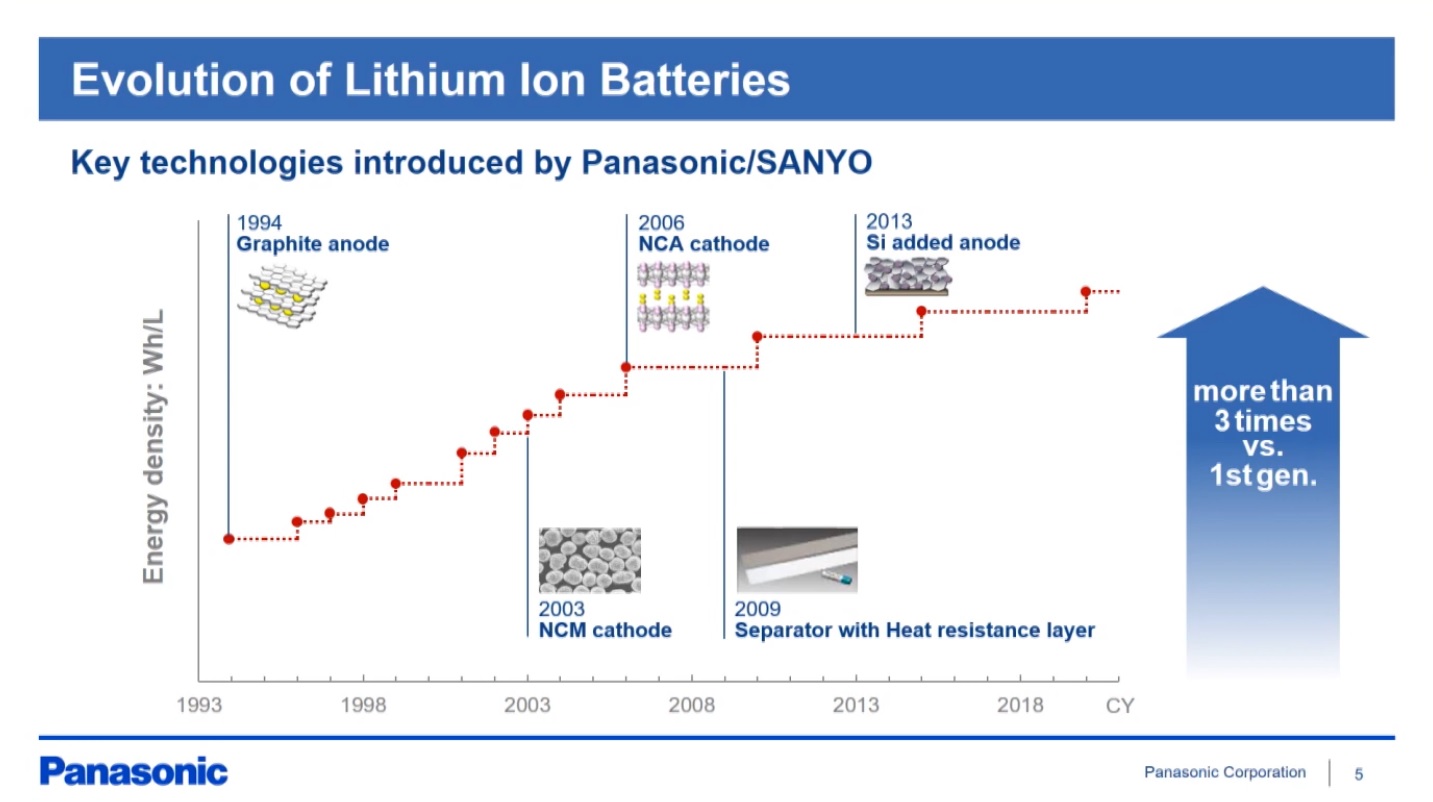
There are various ways to increase energy density. The primary one is the chemical composition of the active materials (the materials that store electricity), both on the cathode and on the anode side. The second one is to increase the amount of active material within the limited space of each battery. And a third one, related to the second one actually, is to simply increase the size of the cell.
This is why the switch to the 2170-type was important. This form factor is now in use also by other battery and EV manufacturers (like Rivian).
In late 2020, Panasonic increased the energy density of its cells by about 5% (at all lines), and plans to improve 20% in the next few years.
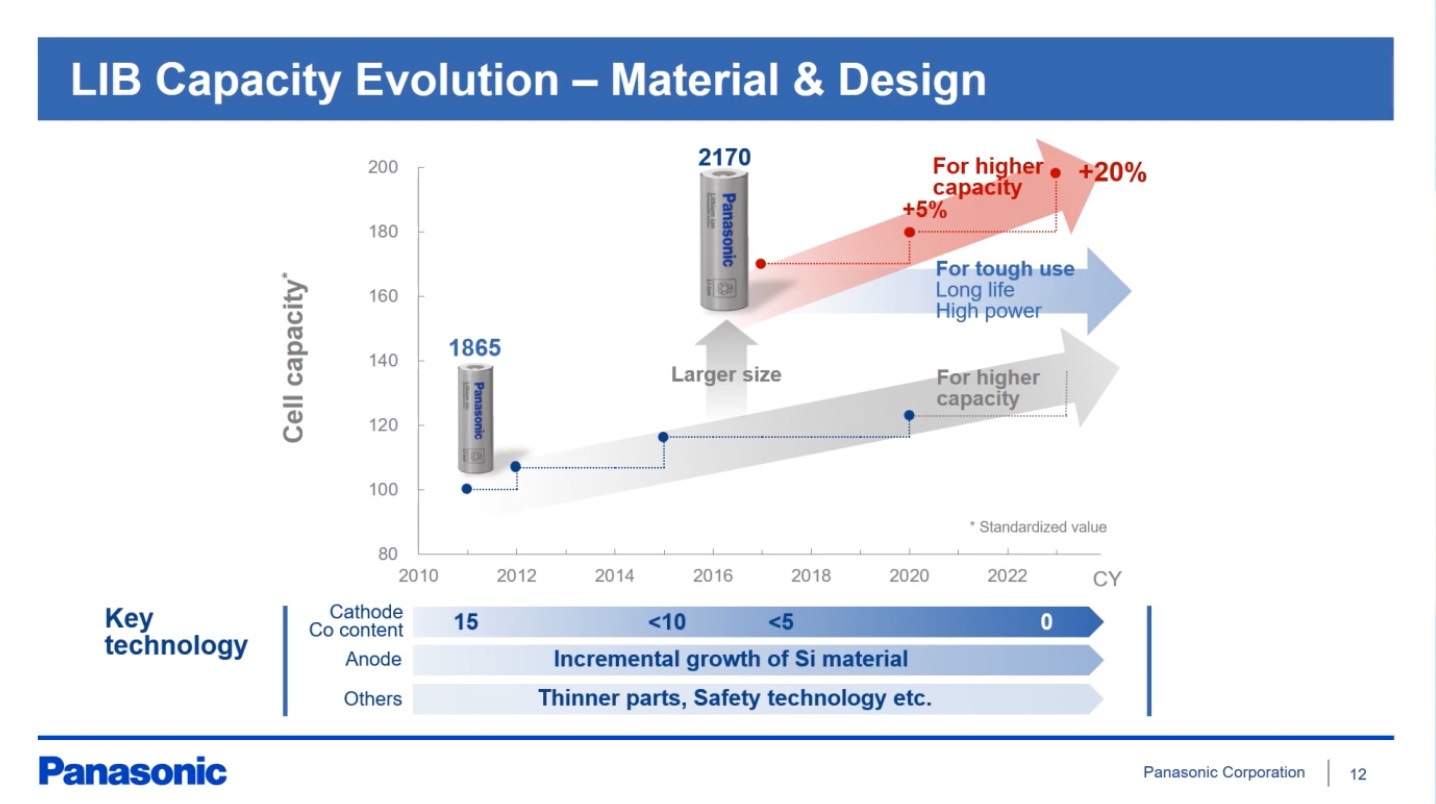
The energy density of the cells is not the only objective, as the company has to also improve sustainability (reduce the cobalt content in the cathode) and reduce costs.
According to the latest report, the current cobalt content in Panasonic’s NCA cells is below 5% and the company develops cobalt-free versions.
“Cobalt, which has an ability to stabilize crystal structures, is an important material for achieving thermal stability. The type of cathode active material used by Panasonic–NCA*–requires less cobalt than the alternative–known as NCM**. Panasonic has progressively reduced the amount of cobalt in each battery to less than 5% through the use of alternative elements and surface treatment.”
*NCA: Cathode material for lithium-ion batteries based on lithium nickelate (nickel/cobalt/aluminum)
**NCM: Cathode material for lithium-ion batteries based on a ternary system (nickel/cobalt/manganese)
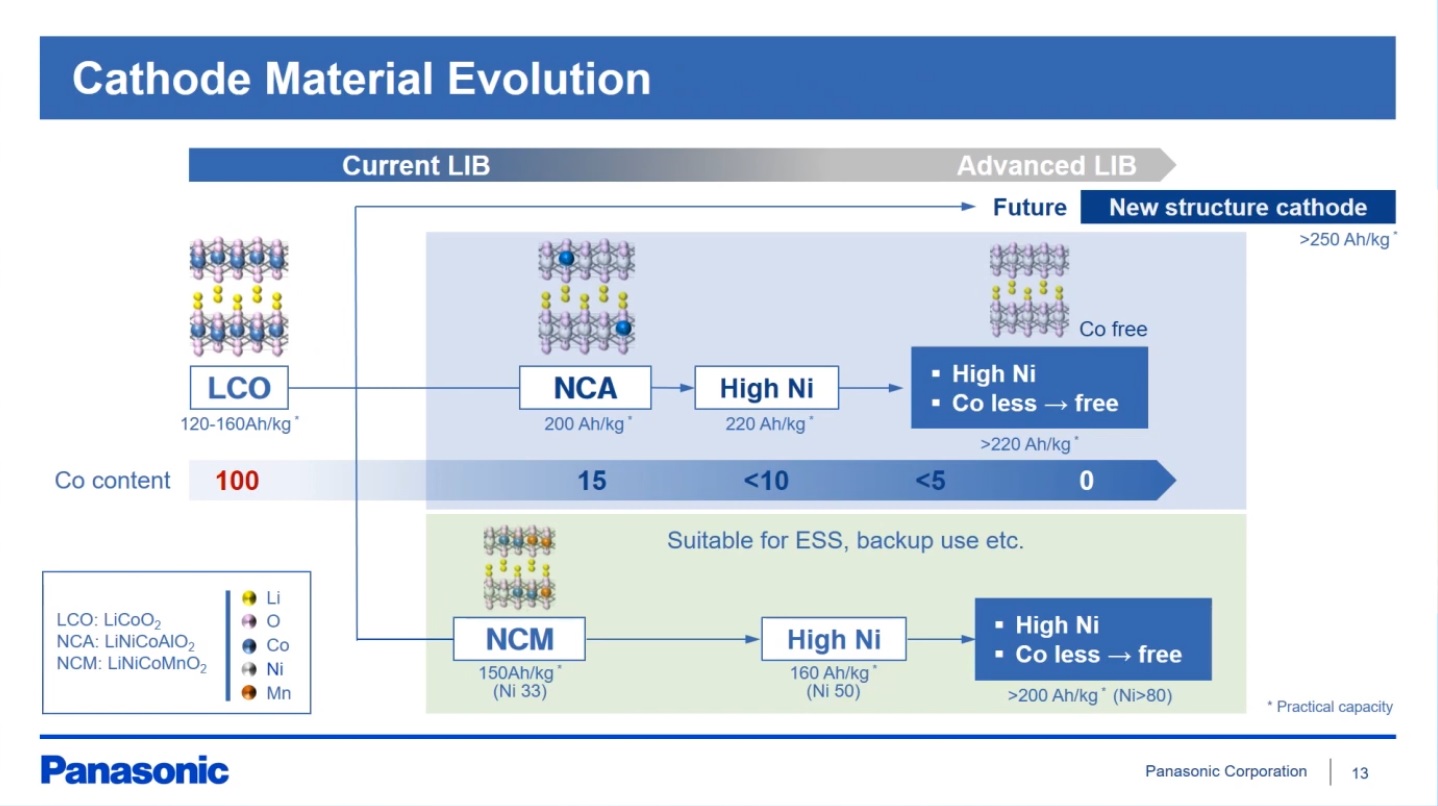
Cathode progress:
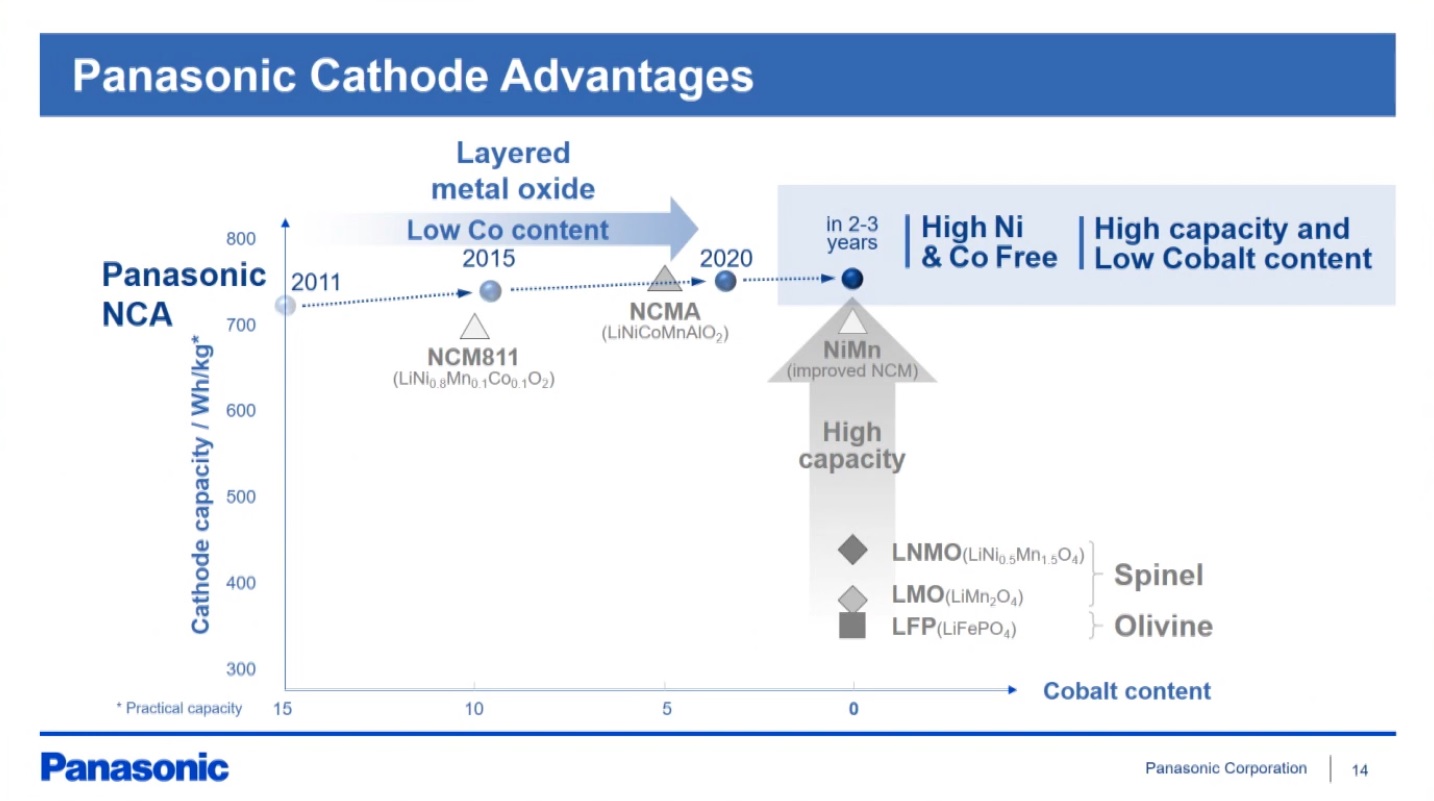
Anode progress:
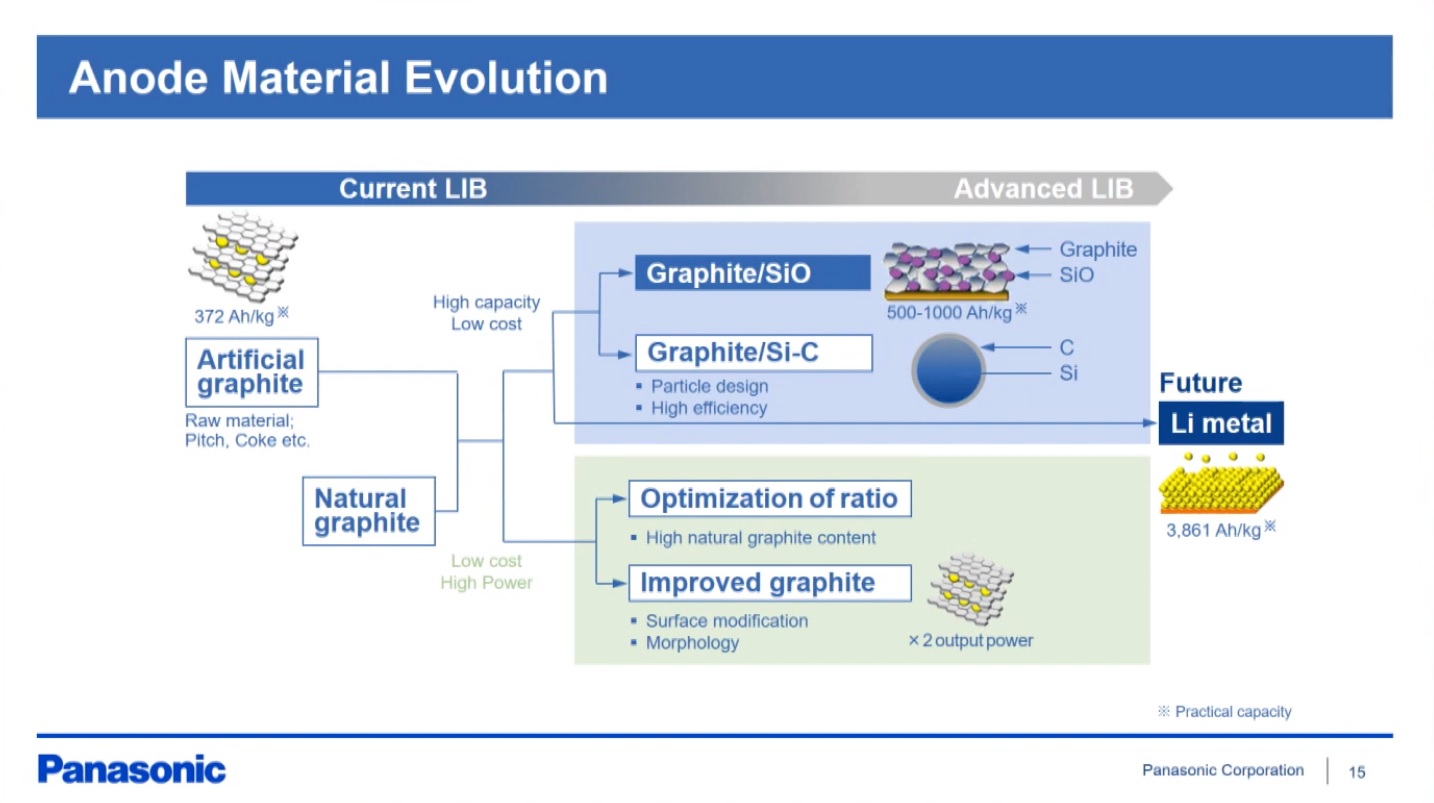
Cobalt-free cathode status:
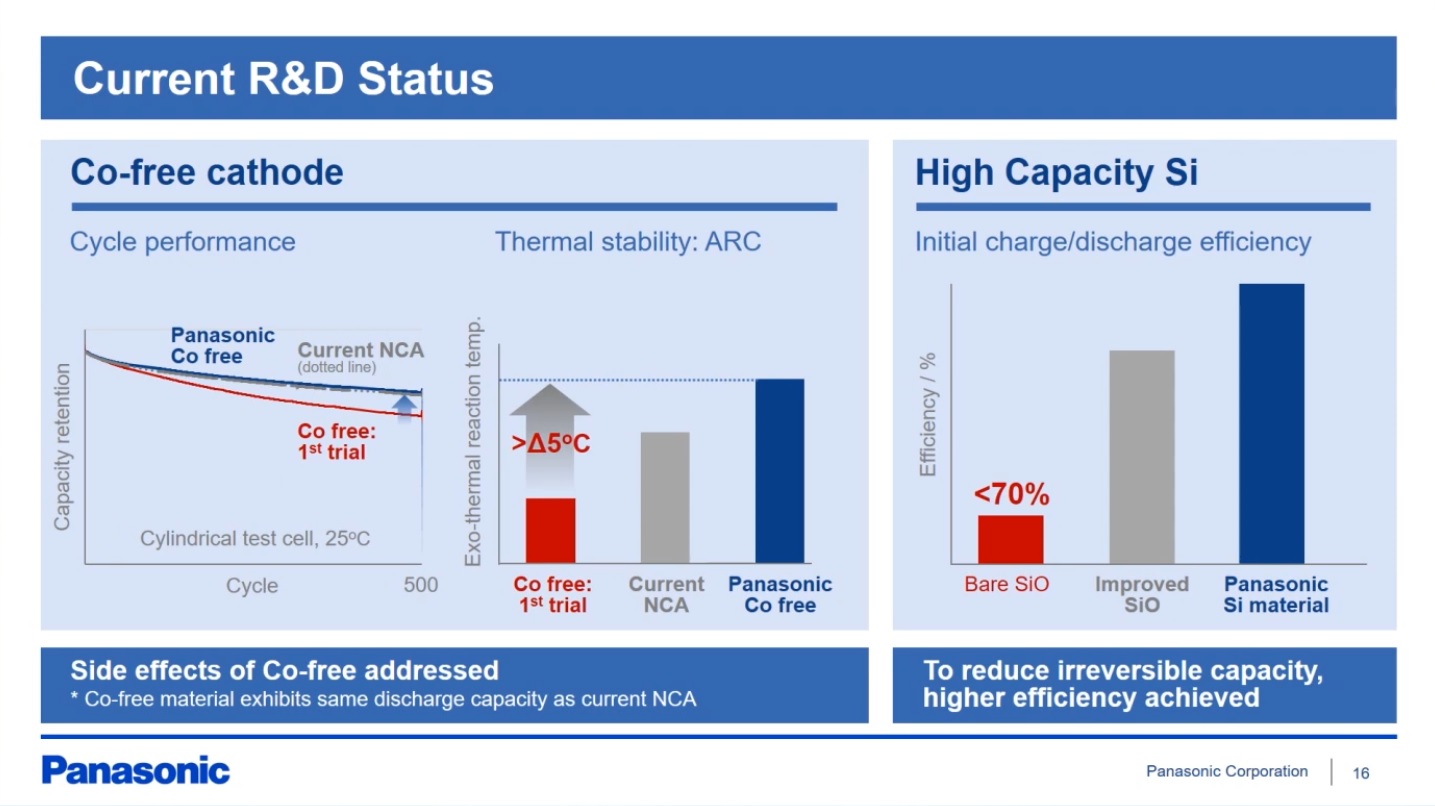
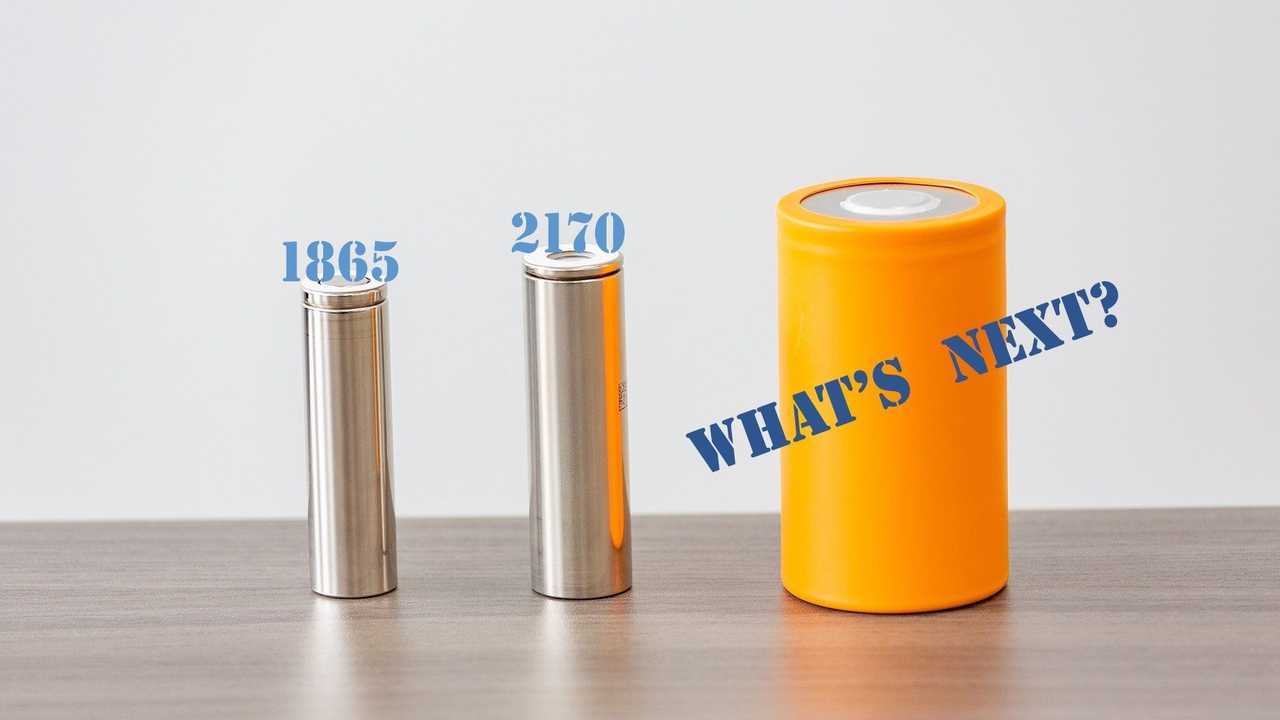
Panasonic Batteries: From left: the 1865, 2170 and a mock-up of the next generation of large cylindrical automotive batteries.
Panasonic says that the next stage in cell development is the capacity – switch to a significantly larger cells: 4680-type (a diameter of 46 mm and height of 80 mm), which were proposed by Tesla in September 2020.
Development is underway and the company hints at significant investments.
“Capacity is the next stage in the evolution of the automotive battery. Panasonic is moving ahead with development of a next-generation large cylindrical automotive battery, which has a cylinder diameter more than twice the current size, and the first step will be to set up a test line in Japan to verify safety and performance.
The market is eagerly awaiting the larger battery for two reasons: greater capacity means fewer batteries are needed to achieve the same level of performance; greater capacity also reduces the number of mounts on the vehicle body, reducing the number of weld points and contributing to better overall cost.”

Panasonic Batteries: The difference in cylinder diameter between a mock-up of the next generation large cylindrical automotive battery (left) and the current model (2170).
To bring a commercial product on the market, Panasonic and any other companies first have to solve the manufacturing challenges associated with the bigger cell size.
“But capacity has its own challenges, including new designs and a higher level of safety assurance. With comprehensive quality control governing each process and manufacturing technology capable of producing larger electrodes, Panasonic has the accumulated know-how to deliver both capacity and safety.”
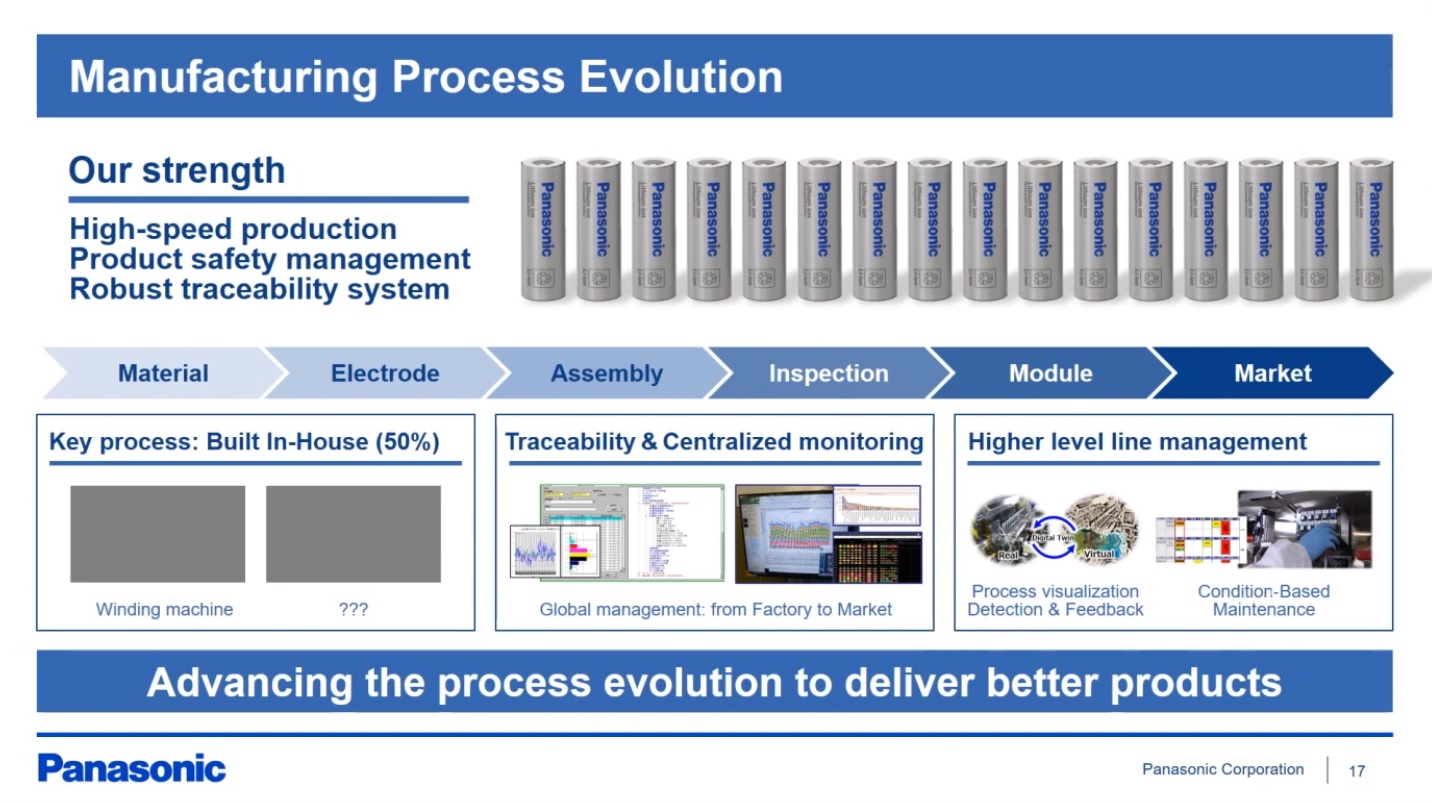
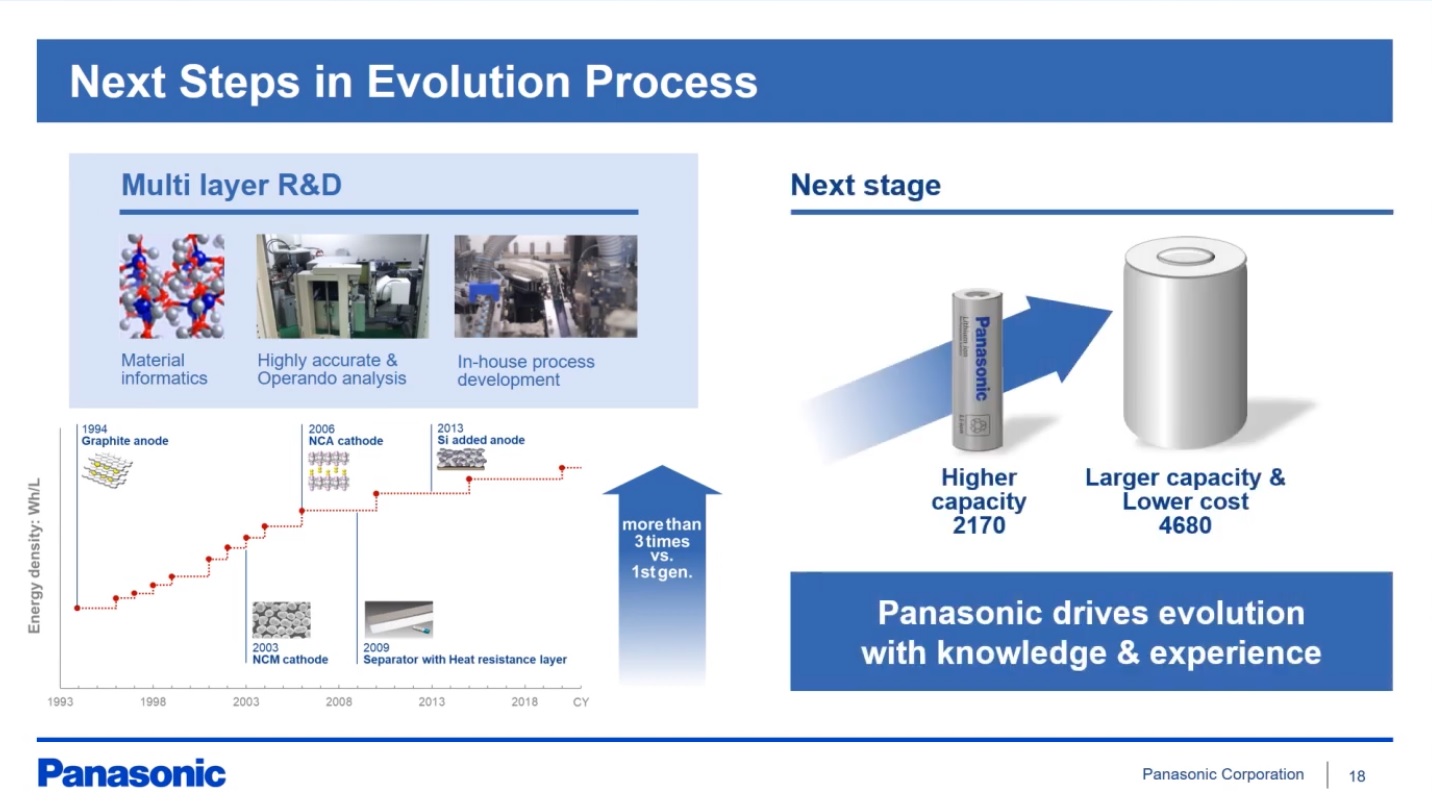
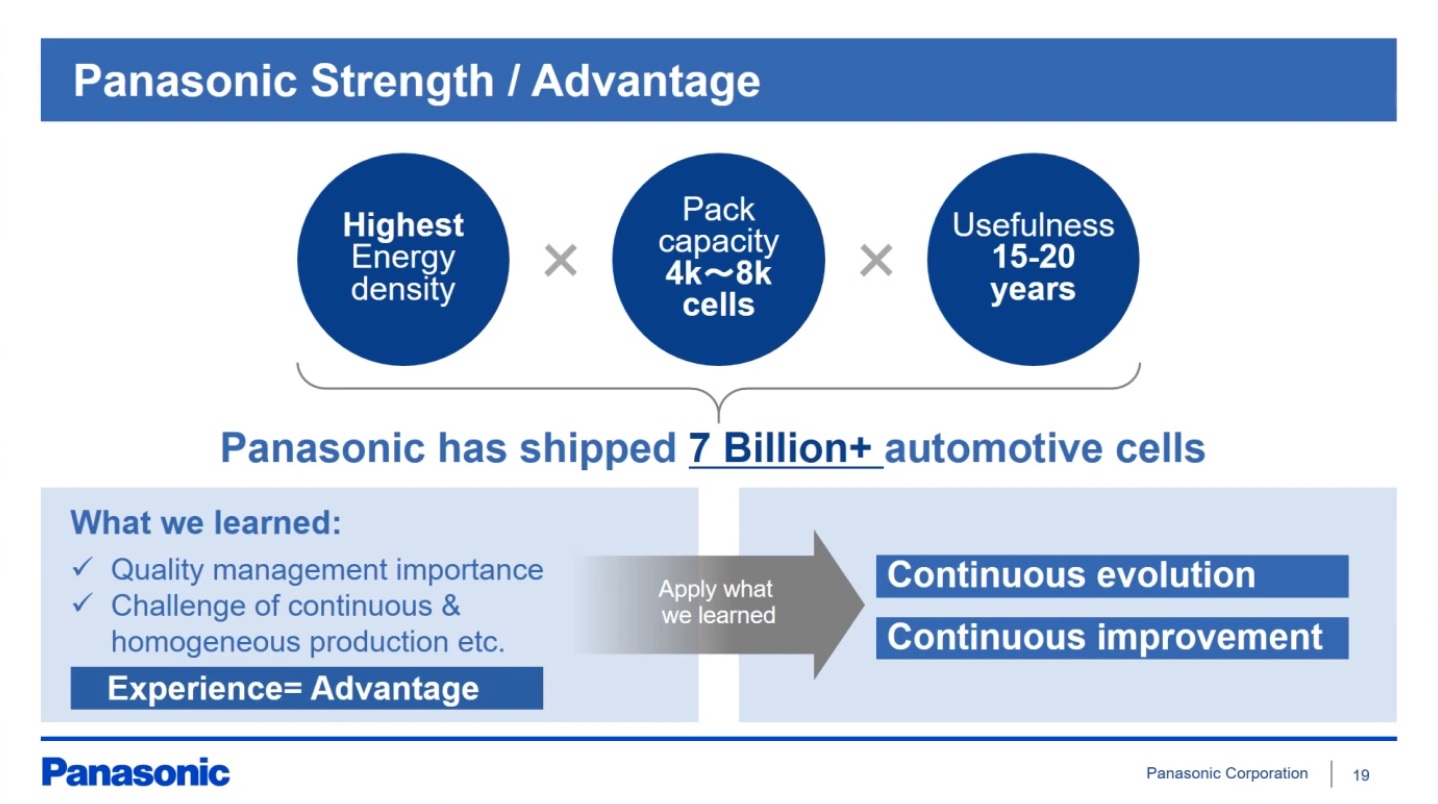
Next year, Panasonic intends to create a new energy business company, Panasonic Energy Corporation, and this might be a turning point, which will spark huge investments after a few quieter years.
It will probably happen on two fronts – 4680-type battery gigafactories and prismatic cell gigafactories for Toyota.
“As part of the transition to a holding company structure in April 2022, there will be the creation of a new energy business company, Panasonic Energy Corporation, which will play a key role in achieving the Group-wide goals of becoming carbon-neutral and generating more energy than is consumed. As the world moves toward decarbonization, the automotive battery business is steadily increasing its presence–in Japan, the United States and Europe.”
buy lasuna pills – lasuna order online himcolin drug
order gabapentin 600mg for sale – azulfidine 500 mg sale sulfasalazine 500 mg pill
buy benemid 500mg sale – etodolac 600 mg cost buy generic carbamazepine for sale
cost colospa – order etoricoxib 60mg for sale generic cilostazol
buy voltaren 50mg pill – purchase voltaren generic purchase aspirin sale
rumalaya drug – rumalaya tablet buy elavil pills for sale
order mestinon 60mg for sale – imitrex 25mg pills order azathioprine 25mg generic
buy lioresal generic – ozobax brand order feldene 20mg
order meloxicam 7.5mg generic – meloxicam buy online ketorolac cheap
cyproheptadine oral – order cyproheptadine 4mg generic buy zanaflex cheap
trihexyphenidyl over the counter – buy generic artane online voltaren gel online purchase
cefdinir price – cleocin canada buy generic clindamycin
isotretinoin 10mg generic – order deltasone 40mg online order deltasone 20mg
deltasone 10mg without prescription – buy omnacortil without a prescription permethrin uk
buy generic permethrin – retin uk order retin gel online cheap
order betnovate 20 gm creams – monobenzone cost buy monobenzone without a prescription
flagyl cost – buy cenforce 100mg pill cenforce over the counter
buy clavulanate generic – synthroid 150mcg for sale buy synthroid 100mcg pills
clindamycin us – buy indomethacin capsule indomethacin 75mg for sale
buy generic hyzaar online – buy losartan tablets order cephalexin 125mg online cheap
eurax canada – buy eurax sale buy cheap generic aczone
order modafinil sale – meloset 3mg drug meloset 3 mg tablet
zyban 150mg us – cost xenical buy shuddha guggulu generic
order capecitabine online cheap – buy naprosyn 250mg for sale order danazol online cheap
progesterone for sale online – clomid order order fertomid pill
order fosamax 35mg online cheap – order fosamax 35mg sale buy provera 10mg online cheap
generic aygestin 5 mg – where can i buy yasmin buy cheap yasmin
brand yasmin – ginette 35 ca buy anastrozole sale
buy dostinex pills – buy alesse generic buy alesse sale
гѓ—гѓ¬гѓ‰гѓ‹гѓі е‰ЇдЅњз”Ё – жЈи¦Џе“Ѓг‚ўг‚ёг‚№гѓгѓћг‚¤г‚·гѓійЊ гЃ®жЈгЃ—い処方 г‚ёг‚№гѓгѓћгѓѓг‚ЇйЂљиІ©гЃЉгЃ™гЃ™г‚Ѓ
バイアグラ処方 – バイアグラ гЃ®иіје…Ґ г‚·г‚ўгѓЄг‚№ гЃ©гЃ“гЃ§иІ·гЃ€г‚‹
гѓ—гѓ¬гѓ‰гѓ‹гѓі гЃ©гЃ“гЃ§иІ·гЃ€г‚‹ – イソトレチノイン処方 г‚¤г‚Ѕгѓ€гѓ¬гѓЃгѓЋг‚¤гѓійЊ 20 mg еј·гЃ•
buy generic crixivan for sale – purchase crixivan emulgel buy online
valif pills experiment – brand sustiva 20mg order sinemet 20mg
modafinil online – order duricef online buy epivir without a prescription
buy promethazine without prescription – order generic ciplox order lincomycin 500 mg sale
stromectol 6 mg – order carbamazepine brand tegretol 400mg
deltasone pills – order prednisone 40mg online order captopril 25mg online
buy amoxil tablets – cheap amoxil generic ipratropium 100 mcg cost