Sponsored by Lubrizol.
The explosion in EV uptake has created huge opportunities for innovations in the vehicle electrified powertrain, and the unprecedented rapid design of completely new lubricating fluids to allow the electrified powertrains to operate at their utmost efficiency.
At the heart of the e-powertrain is the electric motor. Increasingly this is intentionally soaked with the lubricating fluid, which must directly cool and protect this vital component of the vehicle drive.
OEMs are now specifying completely new e-fluids be used in electrified powertrains and the default of taking off-the-shelf Automatic Transmission Fluids (ATF) is rapidly falling out of favor.
Why is this so?
Transmission fluids, including ATFs, can contain additives that are not relevant for e-transmissions. For example, they may contain additives for torque converter clutches which are nonexistent in BEV transmissions. Having a dedicated e-fluid optimized for specific hardware designs delivers optimum performance.
Traditional ATFs could also contain additives that are actually damaging, such as some amount of active sulfur chemistry, which can attack any exposed copper conductors, whether that be the e-motor itself or delicate circuitry in proximity to the fluid.
There is a need for technology that has been designed for the specific transmission, and this is where an e-fluid comes in.
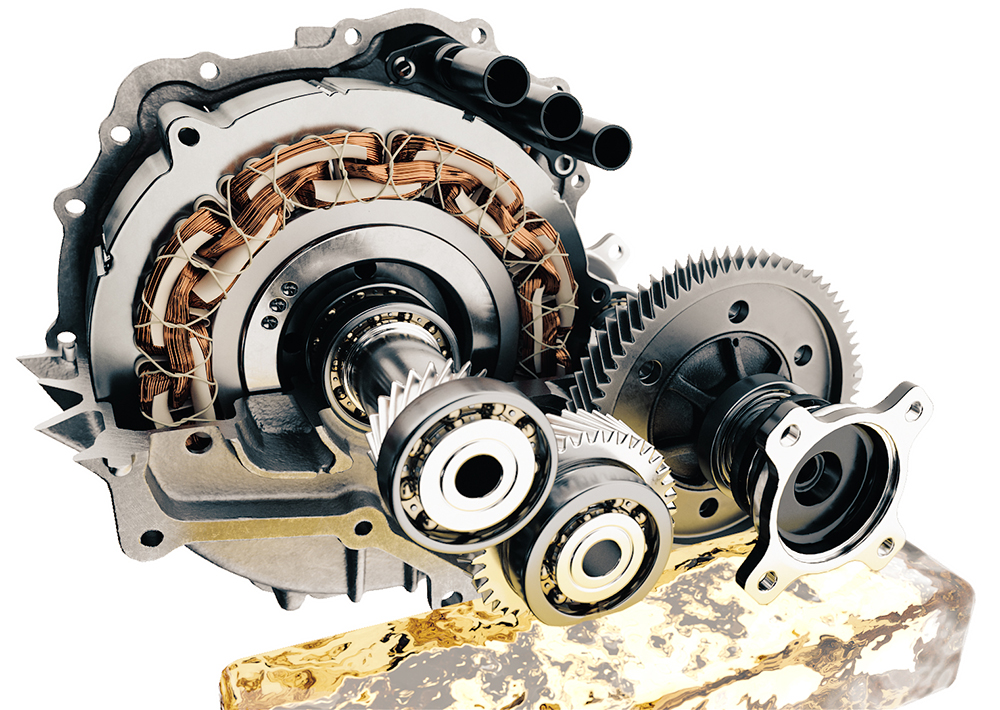
How is an e-fluid different?
“The main differences are the vastly superior corrosion protection ability of the new e-fluids along with the improved viscosity-thermal management characteristics”, says Michael Gahagan, e-Fluid Technology Manager at Lubrizol.
The fluid viscosity is a major impactor on the efficiency of the drive unit and with the OEM wishing to squeeze every km of extra range, the optimal viscosity allows the motor and gearing to operate in the most efficient environment. The electric motor, gears, or bearings do not have to work so hard to overcome viscous resistance from the fluid. Generally, although exceptions exist, e-fluids will have a much lower viscosity than traditional oils.
The need for brand new e-fluid technology was identified early by Lubrizol. Where until recently ATF or boosted versions have been offered to OEMs, such an approach only attempts to mask underlying weaknesses as opposed to delivering the precise fluid technology for the specific hardware design.
Corrosion of electrical devices caused by a fluid that is intended to protect it is unacceptable in the high-tech world of advanced e-powertrain designs. A number of OEMs are adopting a more stable sulfur formulation type for their fluids, lower sulfur, and in some cases “sulfur-free” fluids.
One of the strengths of the new e-fluid technology is its protection of copper, by means of advanced performance corrosion inhibitors and benign antiwear chemistry instead. Traditional fluids from the market simply do not perform as well and have been observed to cause electric motor failures due to corrosion of any exposed copper in the windings from the active sulfur present in the fluid.
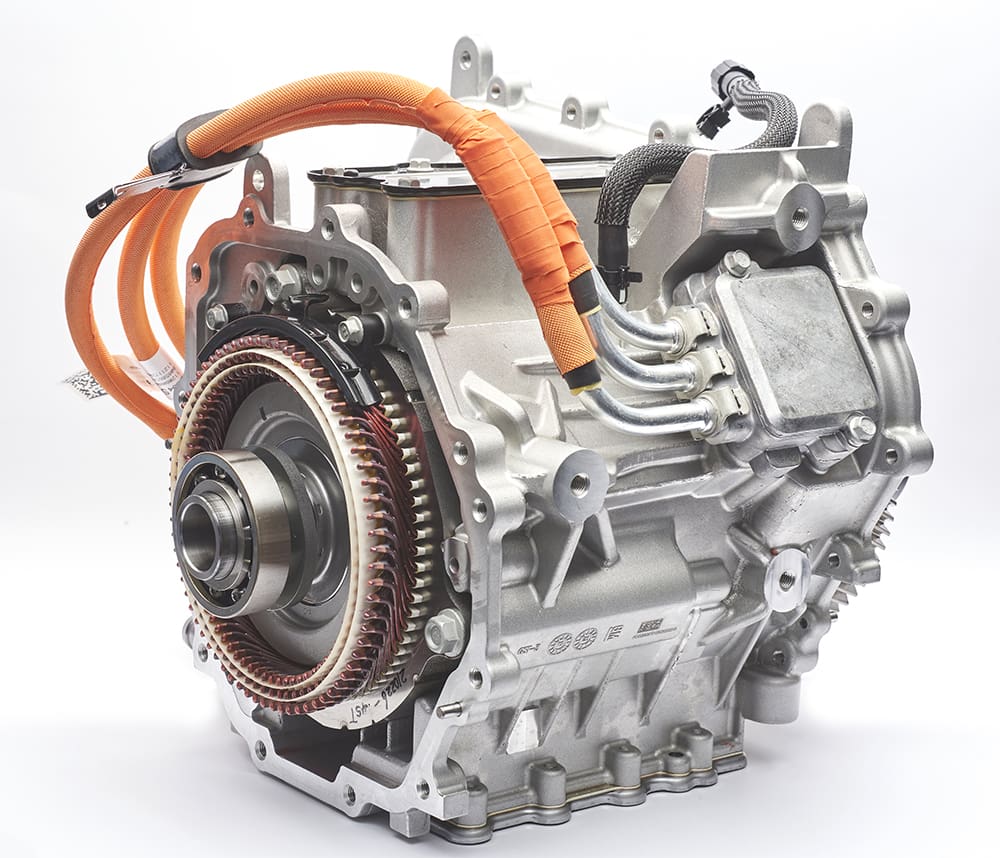
How about gear and bearing protection?
Gear and bearing protection was a worry in the past, especially with lower viscosity. However, the new sulfur-free e-fluids in fact show enhanced gear protection over the traditional ATF benchmarks. These new sulfur-free e-fluids use highly effective gear hardware formulation chemistry that is benign to copper. Active sulfur chemistry can increase the rate of crack propagation in bearings when they start to fail. The new fluid type does not contain any such antagonists and so the bearing protection is excellent.
Cooling with the driveline e-fluid
Although all lubricants are expected to cool, specific cooling aspects of transmission fluids have sometimes been overlooked in comparison to the other performance aspects, with thermal properties such as thermal conductivity and heat capacity unspecified. This is far from the case with the e-fluids. These can cool an electric motor and the windings directly because they flow around all the surfaces, they act to transport heat away and deliver it to a heat exchanger. A dry electric motor misses this advantage as it relies on air to conduct the heat away, which it can only do poorly. The volumetric heat capacity of the e-fluid is enormous by comparison and is beneficial.
Although water has better thermal properties compared with the hydrocarbon-based e-fluid, this cannot be permitted to contact electrics directly due to its higher electrical conductivity. A good e-fluid has a high boiling point and lower chemical activity on insulation making it more suitable as a direct coolant for electrics.
e-Fluids are designed to be better at conducting heat away, by ensuring they have the best possible thermal conductivity, heat capacity, density, and viscosity. By cooling, they lower the operating temperature of the electrical windings making the whole drive unit more efficient as it needs to draw less current. Sometimes called I2R or “copper losses”, the efficiency advantages gained over unoptimized coolant fluids are significant.
By effectively cooling any electric motor magnets, the Curie point (the temperature at which the magnets permanently lose their strength), can be avoided. The fluids perform a vital function in the long-term operation of the magnets. In some examples a more compact design, making the inverter e-fluid cooled and removing the associated water/glycol heat exchanger, is being evaluated as an option.
The other advantage with regards to the oil immersion is the protection of the winding insulation from oxidation by physically excluding oxygen and being itself chemically unreactive to the material. The method for estimating the lifetime of electric motors insulation, according to Dakin and Montsinger’s lifetime models used by the electrical insulation experts, takes temperature factors into account and so the reliability will be improved by better cooling. The life of an electric motor is only as good as it’s insulation, and the e-fluid protects that.
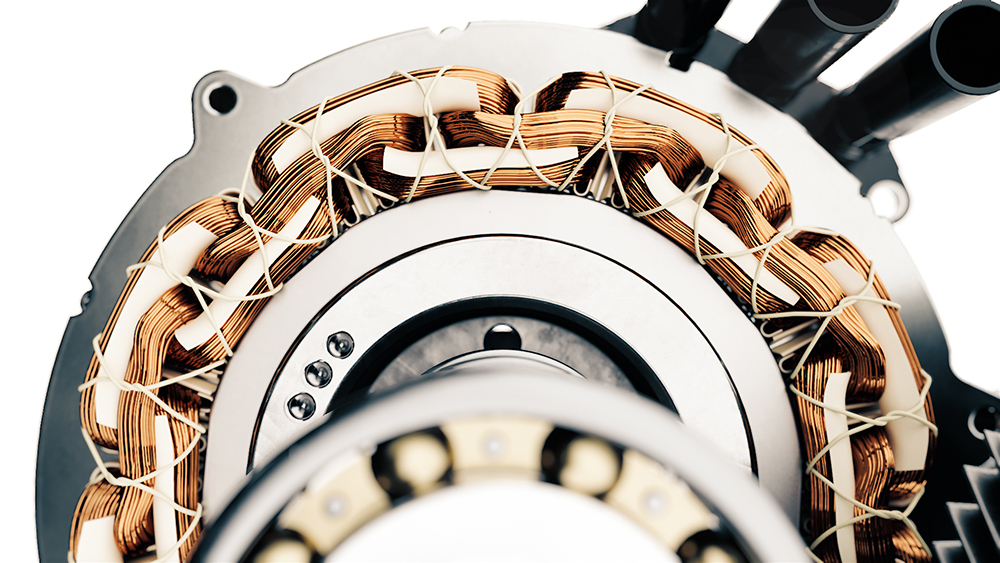
Is it safe to have the e-fluid contacting the electrical circuits?
Having the e-fluid in contact with the electrical circuits is very safe if formulated correctly. The oil protects the electrics as long as it has suitable additives in it that protect them from corrosion. This avoids component, and ultimately, vehicle failure.
Important factors relate to the fluid electrical properties themselves. Generally, the e-fluids are lower in electrical conductivity compared with previous ones, so any fears that electrical currents will pass through the oil and represent a shock hazard are removed. They safely dissipate static electric build up which can be a concern for the protection of semiconductors. They have a low dielectric constant so resolving any chance that significant unwanted electrical charge may be stored by the oil, and they suppress damaging electrical discharges and sparks, because their dielectric breakdown strength is much higher than that for air, for example. The e-fluids are very good electrical insulators and are now viewed as part of the overall electrical insulation system.
What of the foreseeable future?
“If you can look into the seeds of time, and say which grain will grow and which will not, speak then to me”.
Predictions are difficult but the technology will continue to evolve, with many different designs, and the use of increasing voltages to improve recharge times and efficiency. Drive units will become more compact and so heat management from the fluid will continue to dominate. Fluids will increasingly come into to direct contact with electrics and will have to be compatible. Fluid technology will continue to evolve to deliver the enhanced performance for next generation hardware. Innovation will continue.