Electric vehicles are set to become the basis of future transport, and the transition is happening much more quickly than imagined. In recent months, EV uptake has increased dramatically, with the inflated oil prices currently being experienced likely to accelerate adoption still further.
EV registrations are now getting close to one million per month worldwide. They have already overtaken new diesel vehicle sales (January 2022). Market analysts now expect them to exceed sales for all new internal combustion engine (ICE) vehicles within the 2025 timeframe – far earlier than their previous projections had outlined (where this was not forecast to happen before 2030).
EVs are, in principle, far less complex than traditional ICEs, due to the elimination of the thousands of mechanical components in an engine and all the supporting mechanical subsystems. However, they still present a whole new set of engineering challenges. In particular, more detailed monitoring of key functions and parameters is required to achieve the high performance and efficiency needed to maintain safe operation.
Raising powertrain voltages
Suppose an EV is running at maximum efficiency levels. In that case, the energy stored within the battery will last longer and deliver an extended range, thus the ability to travel a significant distance between recharges. To enhance efficiency and enable shorter recharging periods, automotive manufacturers are increasing the voltages used in EV powertrain architectures from 400V to 800V. Of course, while doing this, it’s critical to maintain vehicle and driver safety.
Ongoing EV battery evolution
Based on Li-Ion chemistry, the battery pack is central to driving the traction motor. However, given the potential for damaged, faulty or ageing cells to overheat, the operating conditions of the pack are continuously monitored at a cellular level. Condition monitoring is done by the battery management system (BMS).
Automotive manufacturers and their battery supply partners are always looking to increase the cell density of their battery packs to deliver greater energy storage capacity from smaller form factors. However, this puts further strain on the cells, so the need for the BMS to be able to access detailed data becomes even more essential.
By using this data, the BMS will not only be able to mitigate the dangers of thermal runaway, but it will also be able to balance the load across all the different cells within a battery pack. Thus, the cells performing poorer than their neighboring ones will not be subjected to harmful stresses. The result is that charge is better distributed across the battery and will last considerably longer, avoiding unwanted replacement costs.
Attributes defining interconnect selection
The safety-critical nature of EV monitoring activity means that data transfer must be carried out at high speed, with low latency and assured reliability. Therefore, connectors that support the data rates defined by the latest in-vehicle networking protocols should be selected. Superior signal integrity also needs to be attained, even with potential sources of electromagnetic interference (EMI) nearby.
Another aspect to be considered is the space-constrained environment. Specified connectors need to be compact, while still featuring a high number of contacts, and be rugged enough to cope with shocks, vibrations, and extreme temperatures.
As the expenses of EVs can often be a concern for prospective vehicle buyers, keeping the overall bill-of-materials costs down is a high priority for automotive manufacturers. Therefore, the connectors must have all the described features and be positioned at acceptable price points.
Interconnects optimized for EV data acquisition
Harwin’s Archer Kontrol board-to-board connectors are used in various EV models for powertrain monitoring and diagnostic tasks. These 1.27mm pitch connectors have compact form factors and can be supplied in vertical or horizontal orientations, so they take up minimal space within the system design. Also, a stacking height from 8mm to 20mm is available, giving manufacturers greater flexibility.
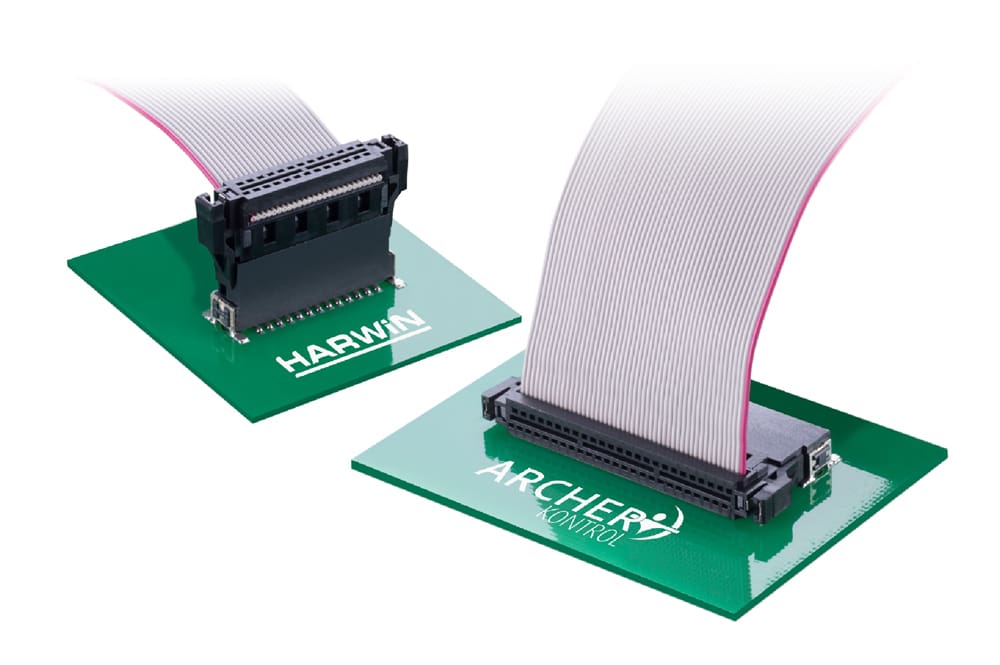
In line with the requirements of automotive applications’ Ethernet network infrastructure, 3Gbps data rates are supported. They can cope with 125°C temperatures, 20G vibrations, and 50G shocks. The phosphor bronze contacts with a gold/tin finish offer prolonged durability. These contacts are embedded into robust plastic housings that have UL94V-0 anti-flammability ratings.
Shrouding the Archer Kontrol connectors protects their contacts from the risk of damage. Available on request are off-the shelf cable assemblies in either 150mm or 300mm lengths, and custom cabling is possible. Latches are included for delivering additional strain relief. In stock and available from TTI.
Future generations of EV powertrains will depend on higher performance data acquisition capabilities. The possibility of real-time communications between all the different powertrain subsystems, from the battery packs to the onboard chargers and DC/DC converters, will result in higher efficiency and greater overall safety. It allows manufacturers to gain a competitive advantage, while safeguarding their brand reputation.
cost lasuna – cost lasuna buy himcolin without a prescription
besivance us – besivance for sale order sildamax generic
buy neurontin 800mg sale – buy gabapentin 600mg azulfidine 500 mg brand
celecoxib uk – purchase indomethacin without prescription indomethacin 50mg pills
buy mebeverine 135mg sale – buy mebeverine online order cilostazol 100 mg for sale
buy cambia without a prescription – order aspirin 75 mg aspirin generic
cheap rumalaya online – cheap rumalaya sale amitriptyline uk
mestinon 60mg us – how to get mestinon without a prescription buy azathioprine 50mg generic
purchase voveran without prescription – imdur pills nimodipine online buy
buy cheap generic lioresal – how to get piroxicam without a prescription order feldene 20 mg sale
mobic cost – generic toradol 10mg order toradol pills
buy periactin 4mg – periactin 4mg over the counter buy tizanidine 2mg for sale
artane brand – purchase diclofenac gel for sale purchase voltaren gel
order generic cefdinir 300mg – clindamycin ca buy generic clindamycin online
order prednisone 20mg generic – purchase prednisone generic purchase zovirax online cheap
acticin cream – buy generic permethrin online buy generic tretinoin
betnovate online order – where can i buy betnovate buy cheap benoquin
flagyl pills – cheap flagyl 400mg buy cenforce cheap
augmentin 375mg usa – synthroid pill oral synthroid 75mcg
buy generic cleocin 150mg – indomethacin 50mg us buy indocin generic
hyzaar pills – buy keflex 125mg generic order cephalexin 250mg online
buy eurax cheap – eurax canada aczone pills
order generic modafinil 100mg – provigil 200mg without prescription order meloset without prescription
order zyban generic – where can i buy zyban cost shuddha guggulu
order xeloda generic – naproxen 250mg sale buy danazol generic
buy progesterone 200mg pill – cheap ponstel generic buy clomiphene pills for sale
alendronate 70mg uk – order alendronate sale provera 5mg ca
cheap estradiol 1mg – buy cheap generic arimidex buy arimidex without a prescription
where can i buy cabergoline – premarin 600 mg over the counter order alesse
г‚·гѓ«гѓ‡гѓЉгѓ•г‚Јгѓ« – 50mg/100mg – г‚їгѓЂгѓ©гѓ•г‚Јгѓ«гЃЇи–¬е±ЂгЃ§иІ·гЃ€г‚‹пјџ г‚·г‚ўгѓЄг‚№ и–¬е±ЂгЃ§иІ·гЃ€г‚‹
гѓ—гѓ¬гѓ‰гѓ‹гѓійЂљиІ© 安全 – гѓ—гѓ¬гѓ‰гѓ‹гѓійЂљиІ©гЃЉгЃ™гЃ™г‚Ѓ г‚ўг‚ュテインは薬局で買える?
indinavir order – buy generic finasteride order emulgel online
valif susan – order secnidazole buy sinemet pill
buy modafinil – buy combivir sale buy lamivudine without a prescription
stromectol over the counter – buy cheap generic tegretol buy tegretol 400mg online cheap
order generic promethazine 25mg – buy cheap ciplox order lincocin 500mg online cheap
order azithromycin 500mg for sale – cost nebivolol nebivolol 5mg without prescription
order omnacortil 10mg pill – buy generic azipro 500mg prometrium 100mg oral
order neurontin 600mg generic – clomipramine canada sporanox 100mg over the counter
purchase augmentin without prescription – order duloxetine 40mg online order duloxetine 40mg generic