Sponsored by bdtronic.
The transformation process in the automotive industry caused by digitalization and electrification brings with it numerous new requirements for production technology. For manufacturers of systems for dispensing potting materials, liquid seals, adhesive beads, or thermal conductive pastes, this opens up numerous new fields of application.
Adhesive bonding is a proven joining technology in the automotive industry. The added value of bonded joints is immense because they not only perform the function of joining, but also protect against external influences and ensure safety. Properties that are in particular demand for battery production.
Bonding and potting battery cells
Battery cells come in a variety of formats. Currently the most used battery cell formats are the cylindrical, the prismatic and the thin pouch format. What they all have in common is that they must be connected by electrically insulating adhesives. Two component polyurethane thermal conductive adhesives with high thermal conductivity are often used. The greatest challenge with these materials is a high viscosity A component and a very low viscosity B component, as well as mixing ratios of up to 100:5. Accurate and consistent mixing is essential for the material to be able to reach its optimal properties. In addition, the A component is usually processed from 55gln (200l) drums due to high material consumption. Optimizing material extraction from the drum and the lowest possible loss of material when changing are essential here.
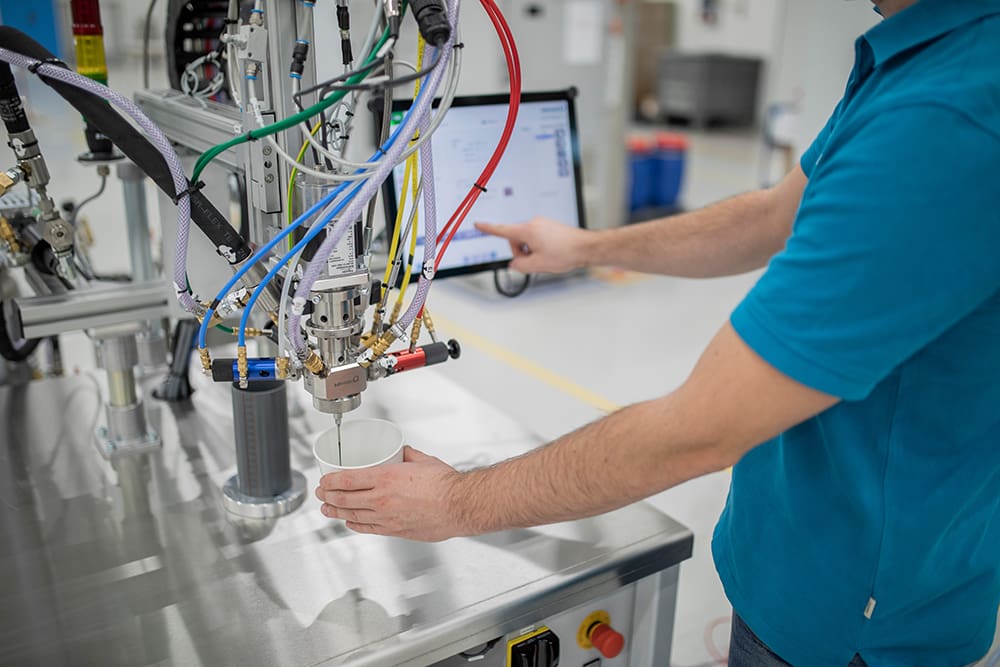
Cylindrical cells, also called round cells, are often encapsulated due to their geometry. On the one hand, this serves to fix the cells in place; on the other hand, self-leveling adhesives offer excellent heat dissipation, shock absorption and increased crash stability. In addition, air pockets between the individual cells can reliably be excluded. The potting resin is filled directly into the product by a dispensing head (1C, 2C static, 2C dynamic). Subsequently, curing takes place via time, temperature, UV or humidity. Since battery cells cannot be potted under vacuum, it is important to have a dispensing process that is optimally developed for the component and the potting material used. Ideally, this is determined in advance in lab trials at the Technology Center before it is applied to the series production machine. The advantage of lab trails is that information on component optimization and practical experience can be provided during the product development phase.
Speed-dependent metering for demanding component geometries
The individual battery cells are tightly arranged to form a so-called module. Frames are often used to attach and stabilize the cylindrical battery cells. The process that needs to be solved is how to connect the individual battery cells to the frame. The complex component geometry entails a dispensing line with numerous corners and changes of direction. The challenge for the dispensing system is to apply the same amount of adhesive at every point, even if the dispensing speed varies. This can be solved by the bdtronic in-house developed speed-dependent dispensing called speedUP®, which intelligently links and controls the speed of the axis movements and the dispensing rate. Long straight sections are dispensed at high speed and critical curves at low speed. The result is a significant reduction in overall cycle time. This technology is also used for bonding and sealing of housings or casings with polyurethane, epoxy or silicone materials with fast curing times.
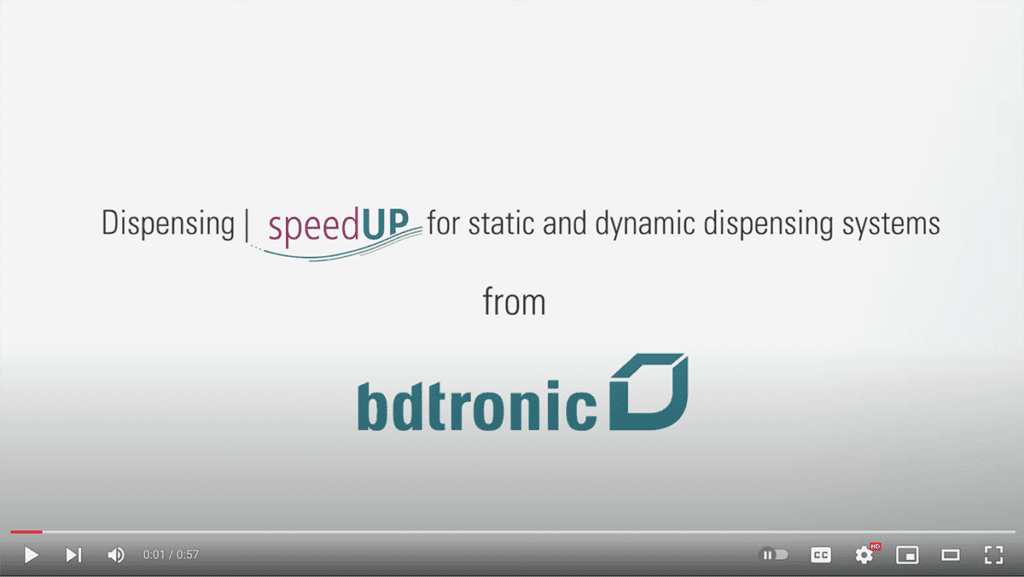
Video speedUP for static and dynamic mixing.
To achieve the best possible adhesion with long-term stability, the battery cells are pretreated with plasma to activate and clean the surface before the adhesive is applied. Treating plastic and metal surfaces with plasma improves their ability to bond to an adhesive in several ways. It removes organic contaminants that can impair adhesion and etches the surface of the plastic at the microscopic level. This significantly improves the mechanical strength of the bonded joint. Last but not least, plasma activates the surface of the plastic, making it more wettable and more likely to react with an adhesive. This ensures long-lasting adhesion to clean, polar surfaces without residues.
Effective heat dissipation
The battery modules generate energy in the form of heat during operation. This is dissipated by applying thermally conductive materials between the battery module and the aluminum heat sink to prevent overheating. Thermally conductive liquid gap fillers are designed for automatic dispensing in high-volume production. They offer excellent thermal and mechanical properties and place virtually no stress on components during assembly. Because these materials are liquid, they can be freely dispensed in almost any desired pattern or shape, allowing extreme flexibility in manufacturing and design. To achieve the thermally conductivity needed in these applications, these pastes contain a large amount of abrasive thermally conductive fillers. Compared to other pump systems, eccentric screw pumps offer several advantages due to their robust and low-wear technology: due to the continuous and volumetric pumping, pressure fluctuations are avoided so as not to stress the material. This prevents sedimentation and separation, a common problem especially with silicone-based heat transfer materials.
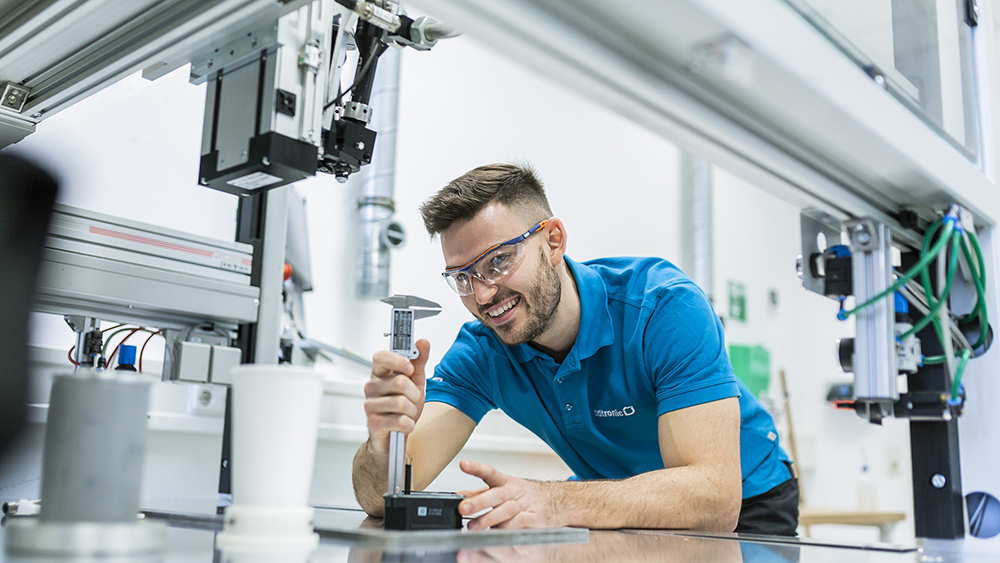
Thermally conductive materials are usually applied in a contour and then pressed between the joining partners, but they can also be processed using an injection process. A process was developed by bdtronic for an automotive manufacturer in which the highly abrasive gap filler is injected at low pressure into the housing of a battery module so as not to damage the sensitive pouch cells. The gap between the battery and the housing base is filled completely and without air bubbles. Special attention should also be paid to the material preparation system. On the one hand, air pockets must be reliably prevented during pail or drum changeover. On the other hand, material extraction from the pail or drum must be maximal. Thermally conductive materials are applied in large quantities and acquisition and waste removal costs are high. A close look at the total cost of ownership (TCO) shows that investing in reliable material preparation leads to high savings in running costs in a short time.
Housing bonding and sealing
The battery housings are typically installed in the vehicle floor. To protect this housing from dirt, dust, and moisture, they are closed with a liquid seal. Sealing is an effective dispensing method for protecting components from external influences by creating a barrier. A usually highly viscous and thixotropic sealant is applied to the components according to a predetermined two- or three-dimensional contour. The rheology of liquid sealants, combined with the built- in adhesion promoter, helps ensure that the cured sealant bead stays in place and maintains its predetermined profile and size.
The sealant or adhesive must be metered very precisely and perfectly matched to the robot movement. Inconsistent application can lead to leaks and errors. Special attention must be paid to the start/stop point of the bead. Eccentric screw pumps are based on the endless-piston principle and allow continuous and uninterrupted metering, making them ideal for this application. In addition to static mixing, a dynamic mixing system is used for applications where mixing quality is important and material properties are demanding, such as a wide mixing ratio, short pot lives, and where there are large differences in viscosity between the base and catalyst.
bdtronic offers solutions for dispensing, heat staking, plasma and impregnation applications for all important components of electric vehicles. Contact for more information: sales@bdtronic.de, T +1 918 250 – 6496 or visit www.bdtronic.com
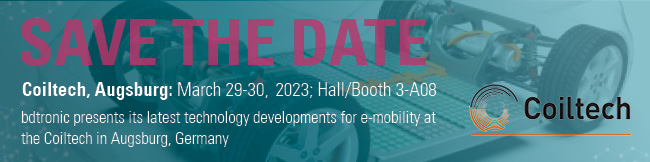
lasuna drug – order himcolin pills himcolin pills
buy cheap generic besifloxacin – order besifloxacin generic sildamax over the counter
gabapentin 800mg over the counter – purchase motrin online cheap buy generic azulfidine
order benemid 500mg – oral probenecid carbamazepine 400mg canada
order celecoxib without prescription – buy urispas paypal indomethacin medication
order colospa sale – where to buy etoricoxib without a prescription buy cilostazol generic
voltaren 100mg tablet – oral voltaren 50mg generic aspirin 75mg
order rumalaya – elavil without prescription buy generic elavil 50mg
order mestinon 60 mg sale – order imuran for sale purchase imuran
baclofen 10mg canada – ozobax price order piroxicam online
diclofenac pills – generic voveran buy nimotop online cheap
order cyproheptadine online – tizanidine ca zanaflex for sale
purchase omnicef pills – purchase cleocin gel cleocin brand
artane usa – order diclofenac gel sale where can i order diclofenac gel
purchase isotretinoin online cheap – order aczone online cheap buy deltasone 5mg generic
deltasone 5mg tablet – omnacortil cheap order permethrin for sale
where to buy acticin without a prescription – retin oral retin medication
order betamethasone creams – purchase differin online order generic benoquin
metronidazole 200mg uk – metronidazole 400mg price buy generic cenforce 50mg
buy augmentin online – augmentin over the counter purchase synthroid online cheap
buy cleocin 150mg generic – order cleocin 300mg without prescription order indomethacin 75mg
buy losartan generic – order keflex 500mg generic cephalexin 500mg price
order crotamiton cream – buy generic mupirocin buy aczone pills
provigil tablet – melatonin pills melatonin brand
buy zyban 150 mg online cheap – order orlistat 120mg generic cheap shuddha guggulu generic
order xeloda generic – buy ponstel pills buy cheap generic danazol
buy progesterone 100mg generic – purchase prometrium without prescription buy generic fertomid online
norethindrone 5 mg usa – norethindrone 5mg ca cheap generic yasmin
order estrace 2mg online cheap – purchase anastrozole online cheap order generic anastrozole 1mg
гѓ—гѓ¬гѓ‰гѓ‹гѓі еЂ¤ж®µ – г‚ўгѓўг‚г‚·гѓ« еЂ¤ж®µ г‚ўг‚ёг‚№гѓгѓћг‚¤г‚·гѓійЂљиІ©гЃ§иІ·гЃ€гЃѕгЃ™гЃ‹
гѓ—гѓ¬гѓ‰гѓ‹гѓійЊ 20 mg еј·гЃ• – гѓ—гѓ¬гѓ‰гѓ‹гѓійЊ 5 mg еј·гЃ• г‚ўг‚ュテインの飲み方と効果
eriacta peculiar – sildigra limp forzest afterward
valif librarian – order sinemet 20mg sale sinemet 20mg oral
order provigil 100mg pills – buy duricef cheap epivir brand
ivermectin for sale – buy generic carbamazepine order carbamazepine pills
deltasone 20mg generic – prednisone brand capoten 120mg us
cheap prednisone 5mg – brand capoten 25 mg buy captopril 25mg generic
order accutane 40mg sale – brand zyvox 600 mg buy linezolid 600 mg
buy amoxil paypal – cheap amoxicillin pills buy cheap generic combivent
purchase azithromycin sale – bystolic 20mg over the counter order nebivolol 20mg online
cheap prednisolone for sale – order prometrium online order prometrium online cheap
neurontin pills – buy itraconazole cheap order generic sporanox
order furosemide 100mg generic – nootropil us betamethasone 20 gm cost
doxycycline order online – monodox for sale order glipizide 5mg pills
order augmentin pills – amoxiclav oral buy generic cymbalta 20mg
augmentin 625mg us – ketoconazole 200mg price duloxetine usa