- Graphite is a pure form of carbon. Its physical structure allows it to store lithium ions.
- There are three main forms of graphite: spherical graphite is used in non-EV battery applications, whereas EV batteries use a blend of coated spherical graphite and synthetic graphite.
- Graphite is the critical component of all current anode designs. Some advanced designs use a small amount of silicon, which can store more energy. However, the use of silicon is limited by its tendency to expand significantly during charge and discharge, so graphite is expected to remain the main anode material for the foreseeable future.
- The company Graphex occupies a middle position in the supply chain—it buys raw graphite from mining companies, puts it through several purification and processing steps, then sells it to battery manufacturers.
Q&A with Graphex CEO John DeMaio
Reading the EV press, you might assume that lithium, cobalt and nickel are the stars of the battery show—they get a lot of coverage, as pundits debate the relative merits of NMC and LFP cathode chemistries and agonize over looming shortages. Meanwhile, over in the anode, there’s an unsung hero: graphite. This crystalline carbon allotrope is good for more than just pencils—it’s found in every EV battery anode, and producing graphite in the forms needed to build high-performance battery cells is a complex and exacting process.
Graphex is a major global producer and distributor of graphite in its various forms. The company manufactures 10,000 metric tonnes per year of purified spherical graphite for EV battery anodes. It also provides technology for producing coated spherical graphite (CSG) and distributes synthetic graphite. Battery makers use a blend of CSG and synthetic graphite to form Li-ion battery anodes.
Charged recently spoke with Graphex CEO John DeMaio, who gave us an explanation of graphite’s essential function, the current state of the industry, and some trends to watch for the future.
Charged: Perhaps you could start with a rundown of what graphite is all about. What exactly does graphite do in the anode?
John DeMaio: In simple terms, a battery has four major components: cathode, anode, separator and electrolyte. A lot of discussion focuses around the cathode side: the lithium, cobalt, nickel, manganese, etc. The anode side is not that remarkable. That’s almost entirely made of graphite, sometimes a combination of natural and synthetic graphite, and in rare cases, there’ll be a tiny amount of silicon doping. The anode side of the battery is where electrons or ions are stored during charge and moved to the cathode side during discharge. So the properties of graphite that are important are its ability to retain charge and to charge up as quickly as possible. That really is the Holy Grail of battery chemistries: quick charging, plus long endurance, long range and multiple cycle times.
The anode side of the battery is where electrons or ions are stored during charge and moved to the cathode side during discharge. So the properties of graphite that are important are its ability to retain charge and to charge up as quickly as possible.
Charged: Is it the physical structure of graphite that allows it to store the ions?
John DeMaio: Correct. The term graphene gets thrown around quite a lot. Graphene is a single layer of carbon atoms. Graphite is a pure form of carbon—by the time we process it into anode material, it’s 99.95% pure—and it’s the most stable form of carbon. The graphene layer of each particle is pretty much the outside layer or two, and that’s where the ions get stored. That’s where the magic happens, so to speak.
Charged: Do all anodes use graphite?
John DeMaio: Currently, there are some emerging technologies that try to use silicon as the anode material. Silicon has some very desirable properties—it stores significant amounts of energy, it’s very conductive, it’s lighter—but there are some challenges with it. So all the workable batteries that are out there now use graphite on the anode side, and they will for—as we see it—the foreseeable future.
Charged: Why is silicon not yet a viable substitute for graphite?
John DeMaio: I think the biggest challenge is its expansion during charge and discharge. Silicon can grow up to 400% of its original size, and that expansion creates a challenge for the physical properties of battery technology. If you have 800 to 1,800 individual cells that make up an EV battery, if each one expands, obviously you’re going to have a real problem with constraining that. There is also a challenge with what we’ll call the shelf life, the calendar aging of silicon. And I believe during the charge and discharge cycles, there is some change in the morphology of pure silicon.
More: A closer look at silicon anode development
The way graphite gets applied to the anode, the graphite is formed into a slurry, and then that slurry is coated onto a very thin copper sheet. In some battery chemistries, they’re introducing maybe one to three percent of silicon oxide. There are other technologies that are being developed such as silicon nanotubes and other types of additives to go into the anode side, but those are in very small percentages. So, all the projections are that the use of graphite in anodes—natural or synthetic—is stable for the next decade or more although there might be introduction of silicon or other additives to try to enhance the battery performance.
All the projections are that the use of graphite in anodes—natural or synthetic—is stable for the next decade or more although there might be introduction of silicon or other additives to try to enhance the battery performance.
Charged: Does graphite also expand during cycling?
John DeMaio: It does. Natural graphite expands, and that’s one of the challenges that we try to address with the technology. There’s probably a three to eight percent expansion rate in natural graphite over time, and about a three to five percent expansion rate in synthetic graphite. Coating the particle with a microscopic layer of asphalt tends to contain that expansion.
Charged: That’s hard for me to visualize—I envision you charging the battery and the cell’s bulging like a balloon, but that’s not how it works, is it? The actual cell doesn’t expand.
John DeMaio: No, not by any means, but that is definitely a concern. You see that, for example, in your everyday household batteries, when they crack and leak at the end of life. Now, the graphite that is in those batteries is not treated the same as the graphite that goes into electric vehicles, which is why the highest and best use of graphite really is in EV batteries, because of the processing that we do. We purify it to 99.95%, we create as close to spherical particles as we can, and then we coat those particles with a coating that resists that expansion and aids in the ability to compact as many particles as possible into a thin layer.
There’s a lot that goes into not just the graphite technology, but graphite as a part of a bigger ecosystem in the battery. There is a lot of R&D going on about optimizing performance of all the different components and how they work together. There are cylindrical cells, pouch cells and prismatic cells. It’s really up to the battery manufacturers and the automakers as to which physical configuration to use, and then of course the internal chemistry configuration. There’s a lot of moving parts with respect to battery chemistry—there’s lithium-iron-phosphate, then you’ve got nickel-cobalt-manganese. It’s all based on what the battery manufacturers think is the best for their application.
Charged: But the different chemistries apply only to the cathode, right? The anode is almost all graphite in any case.
John DeMaio: That is correct, and we like that!
Charged: Haha, I bet you do! Is there still room for improvement in the properties of graphite?
John DeMaio: Yeah, we’re constantly looking at ways to achieve that Holy Grail—more energy density. Battery tech is always looking for longer range and faster charging, and graphite plays a role in that, so we are constantly looking at ways to optimize the performance of our graphite.
Charged: I see that there are several different kinds of graphite—we’ve got spherical graphite, coated spherical graphite, synthetic graphite. How do they differ, and why do you need a blend of the different kinds?
John DeMaio: Spherical graphite is what goes into non-electric vehicle applications. Electronics, power tools, cell phones, laptops. I’ll walk you through the evolution of graphite from rock form to anode. The miners perform what’s called concentration. They crush the ore, then put it through a process called flotation, which separates the graphite from most of the impurities, and that brings it to about a 95% carbon content, and that’s what we acquire from the mining/concentrators on that side of the world.
That spherical graphite is a less expensive product than its cousin, where we take the spherical graphite and put it through a secondary process called coating—applying that microscopic layer of asphalt to it. That becomes coated spherical graphite, and goes into electric vehicles.
So we acquire 95% material, then we put it through a process called shaping and purification, and the end result of that is spherical graphite. So that’s 99.95% now, and it’s shaped into close to spherical—more like potato-shaped—particles. That spherical graphite is a less expensive product than its cousin, where we take the spherical graphite and put it through a secondary process called coating—applying that microscopic layer of asphalt to it. That becomes coated spherical graphite, and goes into electric vehicles. So that’s the relationship between those two—one is just a further processed version of the other.
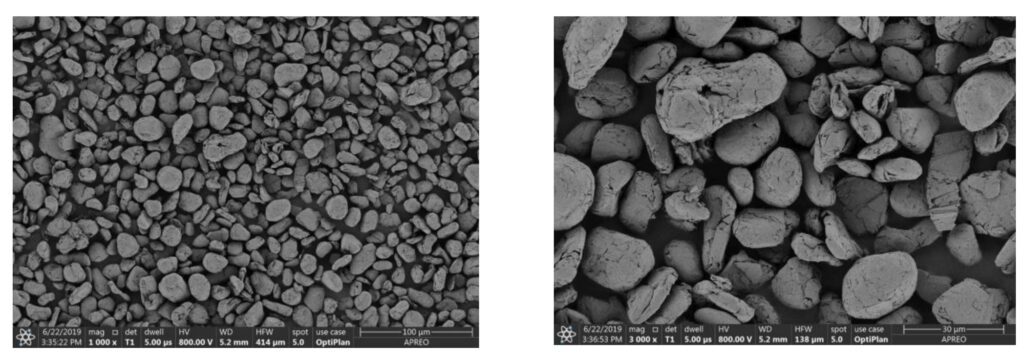
Synthetic graphite is a completely different animal. It’s derived from petroleum coke, from needle coke that’s put through what’s called a carbonization process. It’s carbon, of course, but completely different, and that is one of the pros and cons. It is a little bit better in its expansion performance, but there’s a whole other element to it. It’s a petroleum product. It takes very high energy to create it, and in some philosophical way, it doesn’t make sense to electrify mobility by using petroleum products.
Charged: So what’s the advantage of synthetic graphite?
John DeMaio: Synthetic graphite currently swells less than natural graphite during charge/discharge cycles, which is a desirable attribute for longer cycle life.
Charged: How much synthetic is used in a typical anode?
John DeMaio: It can be up to 50 percent of the anode side. In some cases it’s a hundred percent—it really depends on the design from the battery maker. it’s also more expensive than natural graphite. So, more expensive, higher energy use, much higher carbon footprint, and that’s why I think there’s some pressure on the use of synthetic and why we are trying to develop processes and technologies that will enhance the performance of natural graphite so that synthetic is not needed, if possible.
Charged: So a typical anode for an EV battery would use a mix of coated spherical graphite and synthetic graphite. Is there an optimal mix, or do different battery makers use different mixes to achieve different characteristics?
John DeMaio: The latter. Battery manufacturers are constantly looking at different mixes of graphite on the anode side, different configurations on the cathode side, different electrolytes, all those components. They’re looking at every parameter and trying to optimize the performance that they’re after, and quite frankly, the cost. Because most of the vehicle cost is in the battery, as we all know, so it depends if it’s a high-end vehicle versus a more moderately priced vehicle—that will affect battery chemistry and other components as well. So the mix of graphite varies by manufacturer, by car model, etc.
Charged: What about future battery technologies? Solid-state, lithium-sulfur, sodium batteries—would all of these still be using graphite in the anode?
John DeMaio: Some of them will, and we’re looking at all the ones you mentioned. There’s also pre-lithiation of the anode which is kind of preloading it with lithium ions. There’s a lot of things being looked at, and we of course keep our finger on the pulse. We have our own R&D group that looks at these emerging technologies. How do we play a role? Can we contribute to the development? We have over a decade of experience in this arena, so we can work closely with the battery manufacturers to share what we know, and what we can potentially do together in the future to bring some of these technologies to bear if they truly make sense. Sodium batteries, for example, may have great cold-weather performance. We look at all those things, but there’s a long runway for those new technologies to be perfected, tested and ultimately adopted. So, we’re going to continue to stick to our knitting for at least the next decade, while at the same time, working closely with the battery makers as they develop these new technologies.
The largest graphite mine in the world right now is in China, up in the northeast province. Usually it’s a strip mine kind of an operation.
Charged: As you know, supply chains are a hot topic in the industry these days. Can you take me through the typical journey of graphite from the mine to the battery? What processing steps are involved and where do those take place?
John DeMaio: The largest graphite mine in the world right now is in China, up in the northeast province. Usually it’s a strip mine kind of an operation. The first process is crushing and then flotation—that usually happens either right at the mine or very close to the mine, because there is a fair amount of tailings, so you don’t want to be carting that too far.
After they’re done with their concentration, now you have 95% purity of carbon in this material called flake graphite, or concentrate, and that’s the material that companies like ours will purchase for further processing. We bring in the flake graphite, we run it through what’s called a shaping process, which is a series of mills that bring the particles to a shape and size that is desirable for use in battery anodes.
Then we purify it down to 99.95%, and that happens at our plant—we have a plant fairly close to the mine in China, up in Heilongjiang Province near Jixi City. Then at that point, we either sell it as anode material for non-EV applications, or we send it through a second process, also in that same area, for the pitch coating. At the end of the pitch coating process, we have coated purified spherical graphite, which is used by EV battery makers.
Currently almost all of it is consumed by companies in China, as the EV marketplace in China is probably 15 years ahead of the rest of the world.
Charged: So, you’re shipping that material from China to your customers, the battery makers, which are located where?
John DeMaio: Currently almost all of it is consumed by companies in China, as the EV marketplace in China is probably 15 years ahead of the rest of the world. So there’s plenty of absorption there. But, while we’re on the subject of supply chain, we’re developing a plant in Warren, Michigan. What we are doing is creating the same kind of ecosystem that exists in China, where you have the mine, the processing, and the customer base all intramural, let’s call it. There’s no overseas shipping, etc. it’s pretty self-contained from mine to anode.
We here at Graphex and the entire country are now looking to create, as close as we can, a similar ecosystem here, where you have mining, processing and battery manufacturing all in North America. We know that there’s a lot of gigafactories being built in the States now, or that have been announced and are going to be built. That represents the end use. We’re addressing the midstream, the car companies and battery companies are addressing the downstream, and the missing element is the upstream, the mines. Because there really is no graphite mining currently happening in the US.
We’re addressing the midstream, the car companies and battery companies are addressing the downstream, and the missing element is the upstream, the mines. Because there really is no graphite mining currently happening in the US.
So, we are looking to our neighbor to the north—Canada, where there are mining operations that are either currently online or coming online in the near future. That would represent a North American supply chain. We’re looking at mines in Canada, all kinds of mines outside of China. Again, for reasons of logistics, but also because of the geopolitical concerns that we all are aware of. The Inflation Reduction Act requires, to receive the incentives, restrictions on where the critical minerals come from, where they’re processed, etc, so we’re looking at Canada, Brazil, Australia, we’re looking at Southern Africa, Mozambique, Madagascar, Tanzania, for alternate sources of the raw material. Unless or until adequate supply gets discovered and unlocked in the US.
Charged: How many years do you think it will take before we have a substantial graphite ecosystem in North America?
John DeMaio: That’s a great question—there’s a lot of projections for mines to come online in the next two or three years. I would say if they hit their targets or maybe even 50% of what they’re anticipating, in three years, by 2025 or 2026, we’ll see appreciable growth in mining output in North America. Will it match demand? That remains to be seen, because the scheduled demand looks to be upwards of 500,000 tons of graphite by, say, 2028. Will there be that much production online in Canada? Probably not. Will there be that much supply coming from other resources that are not China? Hopefully. So, we keep a close eye on mining operations.
Charged: When we last spoke, you said graphite supply is currently adequate, but Benchmark Mineral Intelligence is forecasting significant graphite shortfalls from 2025. Is that still an accurate description of the situation?
John DeMaio: I would say that’s still the case. I just came back from a Benchmark conference a couple weeks ago, and the predominant message was that there’s a lot of effort in the mining sector around the world, but it still looks like it’s going to come up short, assuming that auto sales projections stay [on track].
Charged: And that’s not just the US? The whole world’s going to be short of graphite?
John DeMaio: Except for China. China’s got an enormous resource there. Now, that said, there is a tremendous demand for graphite and all minerals in China itself.
I think the challenge for the industry in terms of graphite is visibility. Car companies and battery companies are looking for visibility from mine to anode, and not just in small quantities or in short-term quantities, but in large quantities for the long term so that they can meet their production goals and projections, and that’s what’s not really that visible.
More: Documenting the EV battery material supply chain: Traceability challenges
There is one significant mine in Mozambique that looks like a pretty vast resource, and it is actively being mined, but is that enough, and is it dependable? is there enough processing capacity? There is concern looking forward. If you look at some of the Benchmark materials, they’re calling for, I think, 97 new graphite mines to come online between now and 2030 to keep up with demand, and that’s a tall order.
You’re replacing a hundred years of infrastructure from internal combustion with an EV manufacturing model, and at the same time, trying to domesticate as much of that supply chain as you can.
Charged: You also said that automakers and battery makers need to engage directly with suppliers. Do you see that happening?
John DeMaio: They are, yes. It’s happening. Since we spoke, I would say that that activity has increased. I think it needs to increase even further. I think it’s a shift in the paradigm—it’s a shift in the typical way that automakers have procured materials over the last decades and century. We’ve got two things happening at the same time: you’ve got a shift to EVs for one, but at the same time, now you’ve got a desire and not quite a mandate, but close to it, to domesticate as well. So, you’re replacing a hundred years of infrastructure from internal combustion with an EV manufacturing model, and at the same time, trying to domesticate as much of that supply chain as you can.
The car manufacturers and the battery makers have got to get down into the weeds with us and work together to achieve that mine-to-anode kind of continuity, and we represent a big chunk of that, which is where the transformation of graphite dust into anode material happens. We’re a critical component of that ecosystem.
Charged: Any particular companies that you feel are doing a good job in that department?
John DeMaio: I think we’re all trying to finding our way, and it’s not just about finding the raw material. It’s about making sure it’s qualified as usable, and that is a process unto itself. The qualification process to make sure it performs the way the battery chemists and battery engineers want it to—that is a process that just takes time. If you’re the battery engineer, you want to know, is this graphite going to work in my battery? It’s one thing to have it produced in the lab or at pilot scale and then tested to see if it performs. It’s a different thing to have that material run through an actual processing plant which hasn’t been built yet. So there is a little chicken-and-egg that goes on here, and again, we have to work closely together to make it happen.
Right now we can take graphite from the mine in China, process it in China and deliver finished product. That’s not currently what the market really wants. They want non-China material processed in North America, and that ecosystem doesn’t yet exist at full commercial scale, so there has to be some kind of push and pull. If we take, for example, some Canadian graphite, run it through our current process in China, and produce anode material, knowing that when we build the plants here in the States it’s going to be the same technology, so we should get the same result. We’re confident that we can do that. We’ve been doing it for over a decade. And that’s what we’re kind of working through with some of the car companies.
Automakers, their previous mindset was, show me what you produce, and we’ll see if we can use it. But now the industry is saying, look, we’re not going to build multi-billion-dollar plants on speculation.
That’s not just for graphite. Automakers, their previous mindset was, show me what you produce, and we’ll see if we can use it. But now the industry is saying, look, we’re not going to build multi-billion-dollar plants on speculation. We need to figure out a way that there’s hand-in-glove kind of partnerships here, and that’s evolving. So to answer your original question, we’re getting closer to having those conversations.
lasuna order online – lasuna tablets buy himcolin online
besivance online order – purchase besivance eye drops sildamax over the counter
buy generic probenecid 500mg – purchase carbamazepine online buy tegretol 200mg without prescription
buy cheap generic neurontin – purchase azulfidine generic order azulfidine 500mg for sale
mebeverine 135mg us – cilostazol generic cilostazol 100mg brand
rumalaya over the counter – oral shallaki order endep 50mg generic
order diclofenac 50mg generic – brand voltaren 50mg aspirin tablet
purchase diclofenac without prescription – isosorbide order buy nimotop pills for sale
generic pyridostigmine 60mg – buy azathioprine 50mg online imuran cheap
mobic 7.5mg price – buy maxalt 5mg pills buy cheap generic toradol
purchase baclofen generic – buy piroxicam 20 mg online buy generic piroxicam online
generic periactin – order periactin 4 mg pill tizanidine where to buy
trihexyphenidyl brand – purchase diclofenac gel sale diclofenac gel online purchase
order accutane 20mg – accutane 20mg over the counter buy deltasone 10mg pill
oral cefdinir – buy cheap clindamycin cheap cleocin
oral acticin – retin gel sale order tretinoin gel for sale
order deltasone 10mg online cheap – order prednisone 20mg without prescription buy generic elimite for sale
where can i buy metronidazole – flagyl over the counter order generic cenforce 50mg
purchase betnovate cream – purchase differin sale purchase monobenzone
buy cleocin 150mg for sale – indocin over the counter indomethacin over the counter
buy generic crotamiton – buy eurax cream for sale order aczone gel
cozaar without prescription – order generic losartan 50mg cephalexin buy online
buy zyban 150 mg online – order xenical pills purchase shuddha guggulu generic
buy provigil generic – purchase phenergan sale pill meloset
order prometrium for sale – purchase prometrium generic how to get fertomid without a prescription
order xeloda generic – naprosyn us buy danocrine 100mg online
aygestin drug – buy generic lumigan for sale buy yasmin pills
dostinex 0.25mg canada – buy cabgolin generic cheap alesse pills